The Best 3 Warehouse Order Picking Methods for Efficient Warehouse Setup
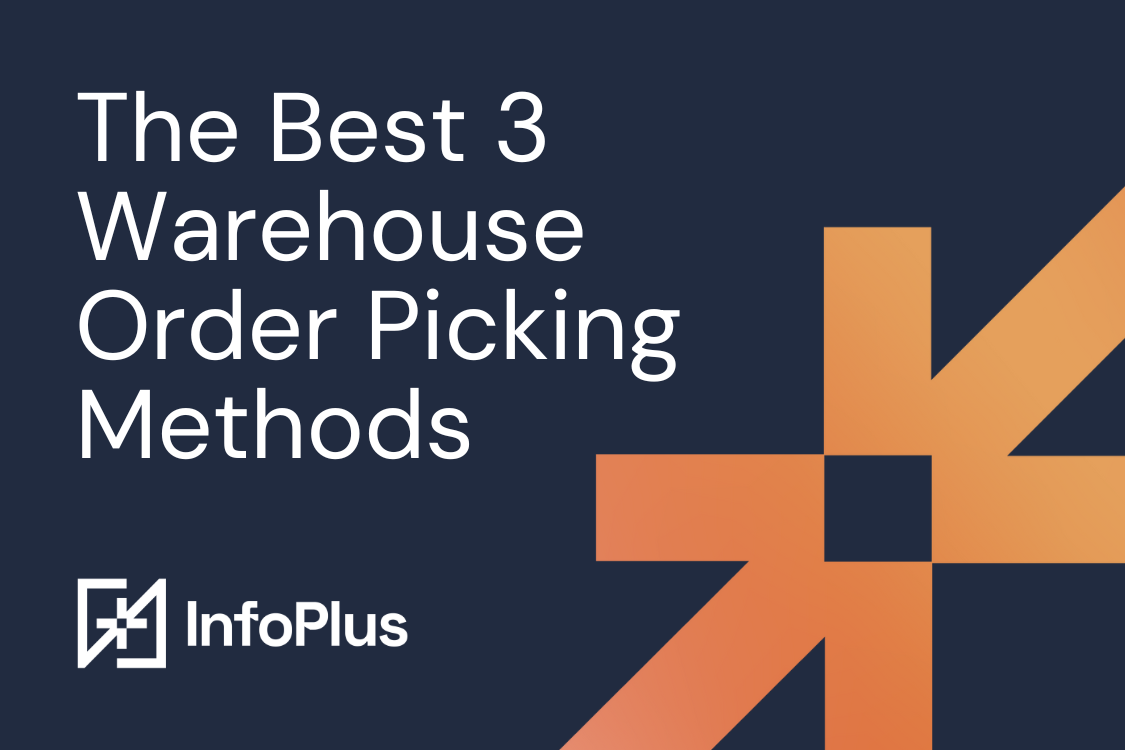
Why worry about which kind of order picking to use when you set up your warehouse? In a nutshell: The order picking method you use on a daily basis will be an essential component of optimizing the speed of your fulfillment, not to mention the layout of your warehouse.
This post will cover three picking methods in wide use, and which one is the best for your warehouse.
- What is Picking Process in a Warehouse?
- How To Improve Picking Order: The 3 Picking Process Types
- What is Wave Picking Method?
- What is Batch Picking Method?
- What is Zone Picking Method?
- Quality Control
- Warehouse Pick Path Optimization and Order Picking Process
- Warehouse Automation
Overall warehouse layout and design of the space, the equipment available to you, your workforce, scheduling, the number of SKUs, and the product itself, all have an impact on the speed and efficiency of various picking methods.
Think of it this way: Your warehouse order picking process determines the speed and accuracy with which products move off the shelves and toward the packing and shipping area—and one step closer to the customer. When the warehouse layout is designed and pick paths are drawn, the picking process may seem straightforward: Simply follow a logical path to pick items off the shelves, package them, and ship them out. But in reality, it’s more complicated. Choosing the wrong method can have workers doubling back, retracing their steps, or crossing paths. It can also delay getting products to your staging and shipping areas, creating bottlenecks. In short, using an inefficient product picking method leads to an inefficient and ineffective warehouse.
Recap: What is Picking Process in a Warehouse?
Order picking is merely the order in which SKUs are pulled from shelves to fulfill orders in a warehouse. Unless a single order is very large, multiple orders are usually pulled at once to reduce trips through the warehouse. There are different ways to organize those trips.
Here’s a way to visualize the idea: In a very small warehouse, every time an order comes in, order pickers can grab items off the shelf and carry them to a packing table where they’ll be wrapped up for delivery. It doesn’t take much growth to make this method obsolete.
Say the business has grown and now ten orders come in at a time. You can walk down the same aisle ten times, fulfilling single order on each separate trip. Or you can walk down the aisle once, picking everything for all ten orders along the way. At first glance, it seems obvious that the second method is better since it will take fewer steps, and therefore less time. But what if the items weigh 100 pounds each? How can they all be picked in one pass?
This simple example illustrates the complexity of picking the appropriate process for a warehouse. The larger the warehouse, the more important your order picking method is. (Fun fact: The average size of a warehouse today is more than 180,000 square feet, compared to 127,000 square feet a decade ago!) Warehouse efficiency hinges on having pickers and machines moving the shortest distance while reducing the number of times products are touched.
How To Improve Picking Order: The 3 Picking Process Types
The three basic order picking methods are wave picking, batch picking, and zone picking. Most warehouses use one or a combination of these three methods.
What is Wave Picking Method?
Wave picking works on the concept of creating a picking sequence that targets individual line items to fill an order in one trip through the warehouse. The goal is to walk less, never duplicating steps.
This might mean walking down a wide aisle collecting items on one side, then them coming back up the aisle picking from the other side. If aisles are close together, perhaps pickers will move in one direction picking from the right and left as they make their way down, then maybe continue to a second aisle. What the actual path looks like doesn’t matter. What’s important is that it flows, saves steps, and doesn’t involve backtracking.
Our example also illustrates the importance of the warehouse layout. In the wide aisle scenario, the picker finishes at the same end of the aisle where they started. In the narrow aisle, their destination is at the other end. Placement of the picker’s destination—the staging or packing area—matters.
Equipment choice is also a factor for a warehouse picking process. Aisle placement must consider the width and turning radius of carts or lift trucks, and whether there will be one-way or two-way traffic. Failing to consider these things could cause traffic jams, bottlenecks, or even collisions. All of which will interfere with productivity.
To better understand the concept of wave picking let’s look at a common real-life scenario of a parent with three children. One child is at swimming lessons, another at band practice, and the third at karate class. Assuming they are all ready to go home at the same time, it wouldn’t make sense to take three trips to shuttle each child home separately. Instead, they will find the most direct route from one place to the next and pick up each child along the way before returning home.
What is Batch Picking Method?
Batch picking uses the wave picking concept, but for more than one order at a time. One pick list combines line items for multiple orders. The picker fulfills the batch of orders in one pass down the pick path or “wave.”
There are two methods to put together the picked orders. In the first, once the entire batch of orders has been picked, the picker delivers them to a staging area. Here the picked items are then sorted into individual orders and prepared for packing and shipping.
Another way to batch pick is to build the orders along the way. The picker’s cart or truck is outfitted with bins that represent each individual order. While they move along the pick path, they will sort picked items into the appropriate bins. Completed orders can go straight from the picker’s cart to the packing area, potentially eliminating the need for a separate staging area.
Batch pickers are limited by the amount that they can fit on their carts in one trip. The size of the cart itself and the number and size of the order bins on it will determine the structure of a batch. Typically, batching works best for orders that include fewer than four SKUs. Filling orders with many different line items may be more efficient with wave picking.
To go back to our parent/child analogy, batch picking is like a carpool. One parent offers to pick up several children along with their own from swimming, band, and karate, and drop them off at an agreed-upon location. They again use the wave picking method to pick the most efficient route. But this time, they load several children into their van at each stop. Once they’ve collected kids from all three locations, they travel to the meetup spot where the other parents are waiting to take them home.
What is Zone Picking Method?
With this picking method, workers are assigned to a specific area or “zone.” They will pick products only in their designated zone, even though an order might include line items from more than one zone. Once picking at a zone is done, those products are delivered to a staging area and combined with things from the other zones. Zone picking is helpful when a warehouse is very large, or when products are very different from one another. For example, there may be a zone for dry goods that is separate from a refrigerated zone.
Wave picking and/or batch picking may be used in conjunction with zone picking. All three picking methods can be mixed and matched to create the most efficient warehouse picking process.
Returning to our analogy, let’s say there are three school buses. One goes to the swimming pool, one to the band practice space, and the third to the karate dojo—three different zones. They each take the quickest route to their destination and pick up all of the kids. Then, they travel to a bus stop where the kids are met by their respective parents who take them home.
Quality Control
One decision to consider when setting up a warehouse order picking process is where to perform your quality control procedures. Pickers can use barcode scanners as they take things off the shelf. Packers might scan things again as they load them into boxes as a second layer of QC.
Two different scans may be overkill, creating an unnecessary step and adding touches to the product. But if there are problems with missed shipments or incorrect orders, multiple QC checks might be necessary.
Location and frequency of quality control should be determined by analytics. The warehouse manager must know the problem areas in order to achieve a balance between quality control and speed. The bottom line is that someone needs to ensure that orders are going out correctly. Where it fits in the process will be up to the warehouse manager.
Automation is Key for Warehouse Pick Path Optimization and Order Picking Process
Creating and implementing an efficient warehouse order picking process is nearly impossible without WMS software and advanced analytics. Without those, a warehouse manager would need to use trial and error to find a method that works. Instead, automated systems can integrate inventory data, workforce availability, equipment capacity, and other analytics. With it, a manager can map out efficient waves and zones, and put together batches for optimum productivity.
The challenge comes in finding what works best for the warehouse and executing the plan. The goal is to create a system that is fast and accurate. Whether using wave picking, batch picking, zone picking, or some combination of the three, the warehouse order picking process must be continually evaluated to optimize efficiency.
Adopting technology correctly takes time and commitment. Luckily, you don’t have to go it alone. Infoplus advises warehouses on what technology they need and how to implement it. We offer guidance on everything from installation, to integration, to roll out and training—and we make sure it’s done right.