Don’t Let Lot Mixing Get You Mixed Up: The How and Why of Mixing Rules
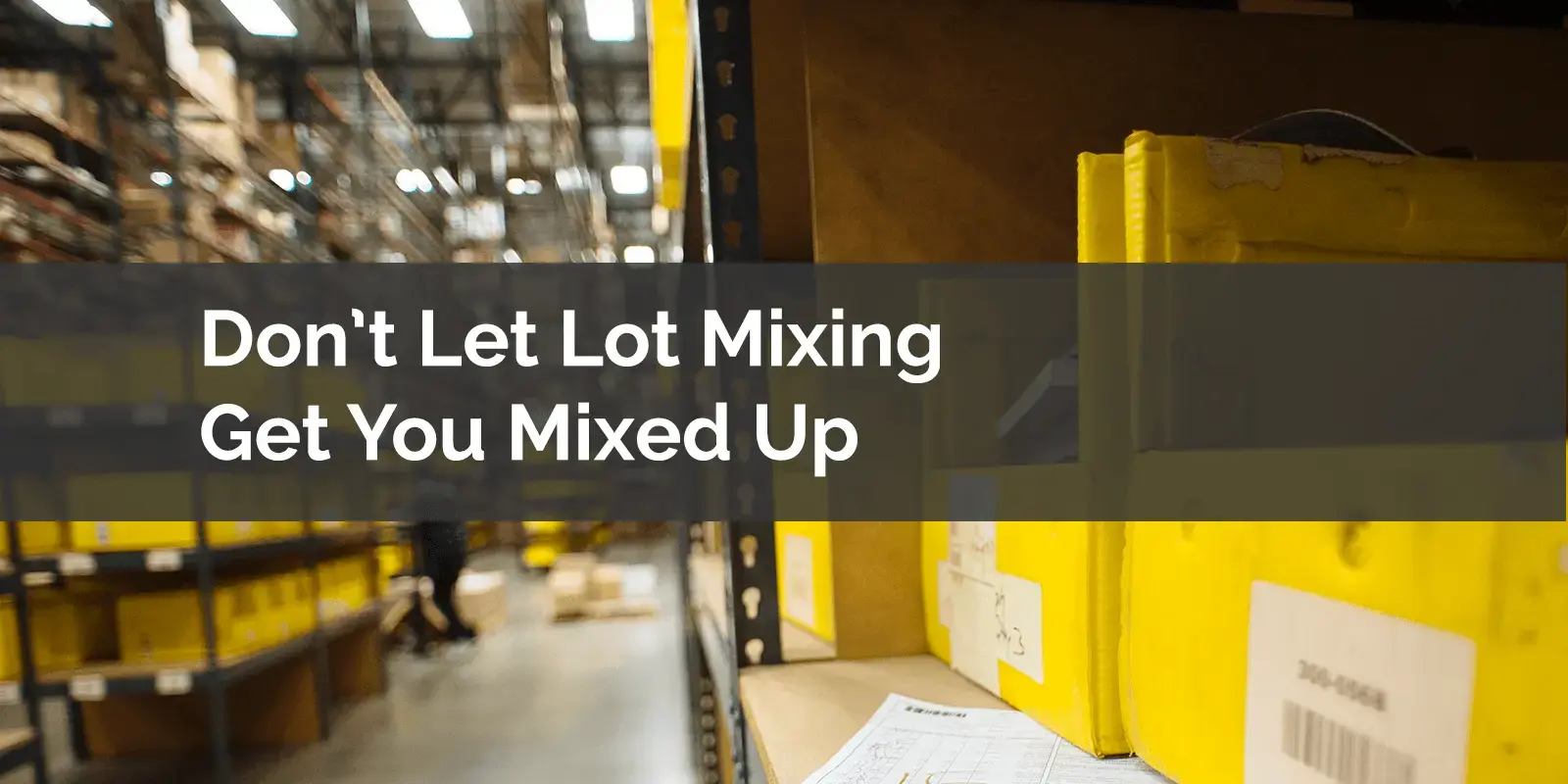
Can last week’s shipment of candles be stored with this week's’ shipment? Can different SKUs be stored with each other? Different lots? When fulfilling orders, should one start with the older stock, or the newer stock? Answers to those questions will not make sense until one understands why and how a warehouse would want to mix and track inventory.
Put simply, storage and fulfillment are essentially games in efficiency: How can a warehouse best receive, store, pick, and ship orders in ways that balance speed and accuracy? Efficiency is a matter of getting the right trade-off. For example, packing all inventory into one space is the most efficient way to use that space. But it would be a nightmare for pickers, not to mention a good way to lose important lot and date information.
This is why mixing rules are important. Mixing rules allow a warehouse or storage facility to specify how SKUs and lots can (or cannot) be mixed. These are critically different from allocation or fulfillment rules, however.
Mixing goods in storage: Lot mixing
When a company carries inventory, items are usually ordered over time as inventory levels change. When new lots are received, a question arises: Can items from the new lots be mixed with existing items from previous lots? The answer to this question depends on the items being stored and the need to keep strict lot control.
Take pharmaceuticals, for example. Pharmaceuticals are highly regulated in the U.S. and most other developed countries. Because there may be potential recalls of specific batches of drugs, warehouses need to keep precise data on the production lot, date, and item receipt or purchase order. Items from different lots, or with different properties, cannot be stored together, because doing so mixes up the items and essentially erases these fine distinctions.
On the other hand, there are many items for which none of this matters. These items are usually mass-produced commodities that change little, if at all, from lot to lot and order to order. To take a simple example, imagine a company storing “value” ping-pong balls. These items are inexpensive, change little from order to order, and have no distinguishing properties. Plus, they can be stored indefinitely. A consumer receiving a ball has no way of knowing if it stayed in storage for two days or two years, or whether it came from China or Chicago.
In this case, the warehouse would do well to find the most efficient way to store the ping-pong balls. This might well include storing items from different lots together to make the best use of available space.
These two cases represent extremes on a spectrum. There may be reasons to track some properties of items, but not others. For example, if you are storing an item with an expiration date, you will want to keep track of production date—but you might not care about exact production lot if a recall is unlikely. This would be the case for storing batteries: Older ones would need to be separated from newer ones, but strict lot control is not necessary.
In a warehouse management system like Infoplus, managers can specify which lots are “allowed” to mix, as well as which items are allowed to mix. This is done by specifying Mixing Rules.
A Lot Mixing Rule uses attributes of an item to control how it can be mixed in a location. Lot Mixing Rules can allocate storage according to:
Item Receipt. By this rule, all inventory in a location must have come from the same Item Receipt/Purchase Order (PO) number. (This is the most strict lot Mixing Rule.)
Inventory Properties. These rules specify that all inventory in a location must have the same “attributes” on their POs (such as production lot, revision date, packaging configuration, etc.). Different PO numbers may be mixed in a single location, however.
SKU. By this rule, all inventory in a location must have the same SKU, but any and all variations of PO Numbers and Inventory Properties are allowed to mix. This is the loosest Lot Mixing rule.
Again, these rules are different from item mixing rules, which allow different kinds of items to be mixed. For example, suppose you want to allow hot dogs and burgers to be stored together in the same location to save space. However, you also want to ensure that no single location contains two different production lots of hot dogs, and that no single location contains two different production lots of hamburgers, so that if there is a recall on a given lot, the items can properly be identified.
In this case, the item mixing rules would allow multiple kinds of items to be mixed in whatever way made for the most efficient storage. But the lot mixing rules would disallow the mixing of production lots for both hot dogs and hamburgers. When done correctly, items would be allowed to mix in the same location, but each item’s inventory properties would not be compromised.
Lot mixing is not the same as allocation
Lot mixing rules are often confused with rules for allocation or fulfillment. True, these two kinds of rules constrain each other—but they are not the same. Lot mixing rules, for their part, specify how items are to be stored.
Allocation/fulfillment rules specify the order in which stored items are to be used in fulfillment. If items are not stored in a way that retains the right information, it might be impossible to use certain allocation rules. (For example, if you use lot mixing rules that allow items from different POs to be mixed, there’s no way to do First In, First Out or FIFO fulfillment.) But, that said, the two kinds of rules are different and need to be thought out carefully on their own terms.
Our next post will look at allocation and fulfillment rules in more detail. In the meantime, if you have questions about any of these rules or how they impact your fulfillment process, contact us.