Demystifying Fulfillment Management Software
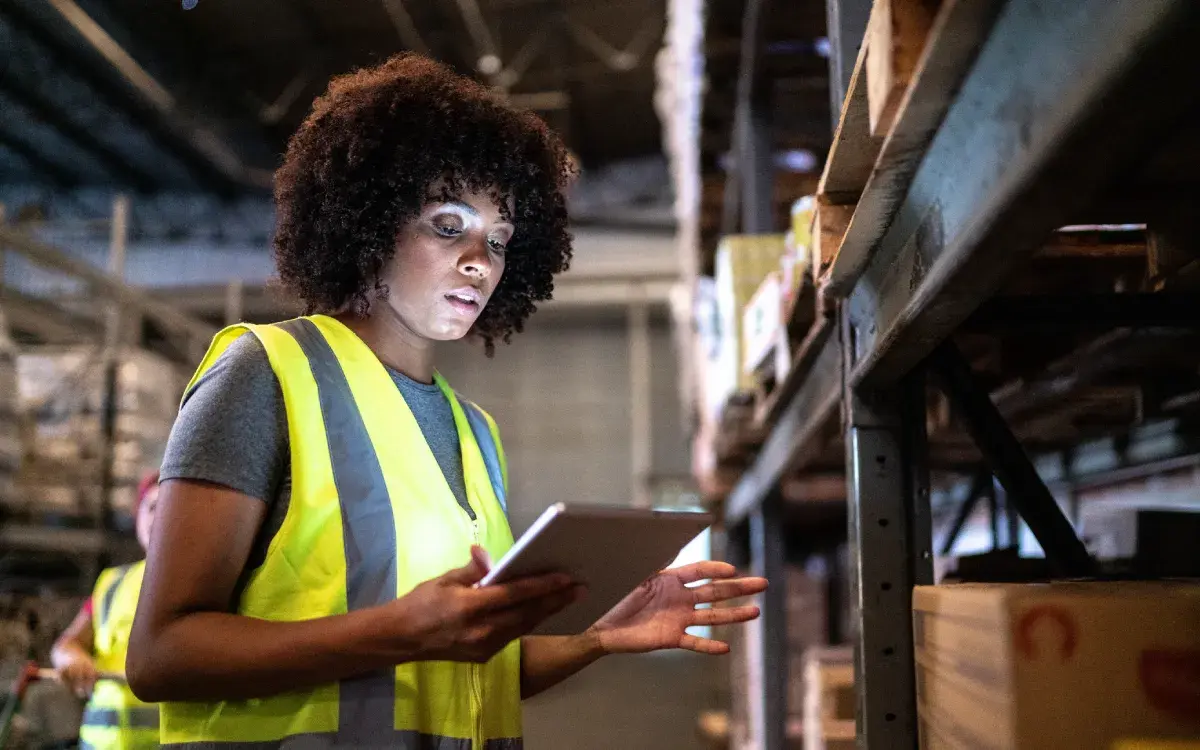
In the ever-changing world of warehouse management, it's easy to feel lost in a sea of industry jargon and buzzwords. One such term gaining attention is Fulfillment Management Software (FMS). But what does it really mean for your business? Ultimately, the question on every buyer's mind isn't about labels or revolutionary concepts—it's about finding the right solution to solve their specific needs.
In this article, we aim to demystify FMS and its relationship with Warehouse Management Software (WMS). Instead of getting caught up in terminology, our focus is on how these solutions can address your challenges and optimize your warehouse operations.
Whether you're considering a FMS, WMS, or some combination of both, our goal is to provide you with the knowledge and insights you need to make an informed decision. With Infoplus, you're not just getting a label—you're getting a tailored solution designed to meet your unique requirements. It's a win-win for your business and your bottom line.
Understanding Fulfillment Management Software (FMS)
Fulfillment Management Software (FMS) are like a specialized version of Warehouse Management Software (WMS) that focus on making sure orders are filled quickly and accurately. They're part of WMS but with a specific job: to make sure warehouses run smoothly and efficiently.
FMS systems have special tools to help with things like deciding the best way to fill orders, keeping track of inventory, and knowing where orders are at any given moment. By using these tools, businesses can fill orders faster, make fewer mistakes, and keep customers happy.
These systems also work well with other business tools like online stores, shipping companies, and accounting software. This means all the different parts of a business can share information easily, so everyone knows what's happening and can make smart decisions.
Plus, FMS systems use technology like artificial intelligence and machine learning to get even better over time. They're always learning and adapting to changes in demand, which helps warehouses stay efficient and responsive.
Overall, FMS systems are a key part of making warehouses run smoothly and efficiently. They work hand-in-hand with other tools to create a seamless system that keeps businesses running smoothly and customers happy.
Shortcomings of Fulfillment Management Software (FMS)
Fulfillment Management Software (FMS) help make the process of getting orders to customers smoother and faster. But, when we compare them to the more complete Warehouse Management Software (WMS), there are some key areas where they don't measure up.
- Narrow Focus: FMS is all about helping with orders — from taking an order to managing stock and making the warehouse work better. But, for a growing business, you might need more, like help with shipping and handling staff, which WMS can provide.
- Integration Hurdles: FMS doesn't always play nice with other business tools and systems, unlike WMS. This can lead to trouble, especially if your business sells through different channels or has more than one place sending out orders.
- Growing Pains: As your business gets bigger, you might find that FMS can't keep up with the increase in orders or the complexities of getting those orders out. WMS, however, is designed to handle growth more smoothly.
- Seeing the Full Picture: With FMS, you get a peek into what's happening in the warehouse and with orders. But WMS goes further, offering detailed tracking and reporting that can help you make better business decisions.
- Less Wiggle Room: FMS usually comes with set features and not much room to change them to fit your unique needs. WMS, on the other hand, offers more options to tweak and adjust things as your business requires.
Even with these limitations, FMS can be a budget-friendly choice for businesses looking to improve how they fulfill orders. However, it's important to think about what your business needs both now and in the future before deciding between FMS and a more extensive WMS solution.
What is Warehouse Management Software (WMS)?
A Warehouse Management System (WMS) is a software application designed to streamline and optimize the day-to-day operations of a warehouse or distribution center. It is a central platform for managing inventory, tracking stock movements, and orchestrating warehouse tasks to ensure efficient and accurate order fulfillment.
Key Functions of a WMS:
- Inventory Management. A WMS provides real-time visibility into inventory levels, locations, and stock movements within the warehouse. It enables businesses to accurately track stock quantities, minimize stockouts, and optimize inventory replenishment processes.
- Order Processing. WMS automates and streamlines the order fulfillment process, from order receipt to shipment. It manages order picking, packing, and shipping operations to ensure orders are processed accurately and delivered on time.
- Warehouse Optimization. WMS optimizes warehouse layout and storage configurations to maximize space utilization and operational efficiency. It provides tools for organizing warehouse zones, bin locations, and picking routes to minimize travel time and labor costs.
- Labor Management. WMS helps businesses optimize labor resources by assigning tasks, tracking employee performance, and generating labor reports. It ensures that warehouse staff are deployed efficiently and that productivity targets are met.
- Integration with Other Systems: WMS integrated with other business systems, such as enterprise resource planning (ERP) software, transportation management systems (TMS), and eCommerce platforms. This enables seamless data exchange and coordination between different departments and systems.
Benefits of Using a WMS:
- Improved Efficiency. WMS automates manual warehouse processes, reduces errors, and increases throughput, improving operational efficiency.
- Enhanced Accuracy. WMS improves order accuracy and reduces picking errors by providing real-time inventory visibility and implementing barcode scanning and RFID technology.
- Cost Savings. WMS optimizes warehouse space, labor resources, and inventory levels, resulting in cost savings through reduced carrying costs and improved labor productivity.
- Scalability. WMS is scalable and can adapt to the changing needs of growing businesses, allowing them to expand their warehouse operations without compromising efficiency.
Overall, a Warehouse Management System is a critical tool for modern warehouses and distribution centers, enabling businesses to streamline operations, increase productivity, and deliver exceptional customer service.
Choosing Between FMS and WMS for Your Warehouse Needs
In the world of warehouse operations, understanding the tools at your disposal is crucial. Let's break down the difference between Fulfillment Management Software (FMS) and Warehouse Management Software (WMS) and figure out which one might suit your business better.
- WMS is your warehouse's command center. It keeps track of everything — from inventory levels to making sure orders are packed and shipped correctly. It's designed to make your warehouse run as efficiently as possible, covering tasks like managing staff, optimizing storage, and integrating with other business systems.
- FMS, on the other hand, is more like a specialist focused on getting orders to customers. It handles the nitty-gritty of order processing, picking, packing, and shipping. It's all about making the fulfillment process quick and error-free, perfect for ensuring efficient order delivery.
When to Lean Towards FMS or WMS
Starting out or running a smaller operation with a limited range of products? An FMS could be your best bet. It's great for when your main goal is to get orders out the door without the need for the extensive capabilities of a WMS.
But as your business grows — think more products, higher order volumes, and complex operations — you'll likely need the broader, more integrated features of a WMS. A WMS is essential for managing a larger operation efficiently, offering advanced analytics, labor management, and seamless integrations that a standalone FMS can't provide.
Why Not Both?
Interestingly, a comprehensive WMS often includes functionalities you'd find in an FMS. This means if you're already using a WMS, you might not need a separate FMS. A good WMS can manage your inventory and orders, streamline operations, and integrate with other systems, effectively covering the key roles of an FMS.
Choosing What’s Best for Your Business: FMS vs WMS
Navigating the software maze for your warehouse or logistics operations demands a clear understanding of the tools at your disposal, particularly when deciphering the roles of Fulfillment Management Software and Warehouse Management Software. It's not about getting caught up in the latest industry jargon but about pinpointing a solution that truly resonates with your unique business needs.
- Real-Time Inventory Tracking: Seek out a system that shines a spotlight on your inventory, offering live updates on stock levels and locations. This not only helps keep stockouts at bay but also streamlines your replenishment strategy, ensuring you're always ready to meet demand.
- Automated Workflows: Efficiency is key, so opt for a system that smooths out the kinks in your warehouse operations. Automation in order processing, picking, packing, and shipping slashes manual errors, boosts your workflow's speed, and enhances overall order fulfillment efficiency.
- Customizable Reporting: Knowledge is power. A system that allows you to tailor reports to your liking can offer invaluable insights into inventory management, order precision, and workforce productivity, empowering you to make informed decisions that propel your business forward.
- Seamless System Integrations: A harmonious software ecosystem is essential. Ensure your chosen solution can easily converse with other critical business systems--be it eCommerce platforms, shipping services, or ERP systems. This integration is crucial for syncing orders, managing stock levels, and ensuring a smooth operation from start to finish.
Scalability and Flexibility: A Balancing Act
Your chosen solution should be a companion for growth, capable of adapting to your expanding operations, whether that means adding new warehouses, diversifying product lines, or navigating market shifts without skipping a beat.
Total Cost of Ownership: Look Beyond the Price Tag
While initial costs matter, the real value lies in understanding the total cost of ownership. Consider not just the upfront investment but also ongoing expenses, training, and potential customizations. Remember, the goal is to find a solution that offers a return on investment through heightened efficiency, minimized errors, and enhanced customer satisfaction.
Vendor Support: Your Safety Net
Lastly, the expertise and support offered by your software vendor can make all the difference. Seek out a provider known for outstanding customer service, regular updates, and a deep understanding of industry challenges. Comprehensive training and reliable technical support are your lifelines for a smooth transition and sustained success.
By taking these factors into account and focusing on what truly matters—functionality and fit—you'll be well on your way to selecting a software solution that not only meets your current needs but also supports your future aspirations, driving efficiency and growth in an ever-evolving marketplace.
Embracing the Power of WMS
In conclusion, while the term Fulfillment Management System may sound enticing, it's essential to recognize that a robust Warehouse Management System inherently encompasses all the functionalities required for effective fulfillment management. By leveraging a comprehensive WMS, warehouse operators can streamline operations, optimize processes, and drive business growth. So, the next time you encounter the term FMS, remember that a reliable WMS is all you need to unlock the full potential of your warehouse.
By demystifying the concept of FMS and emphasizing the importance of a robust WMS, we aim to empower warehouse professionals to make informed decisions and confidently navigate the ever-changing landscape of warehouse technology.
If you’re interested in learning more about how your fulfillment operations could benefit from a WMS, schedule a free warehouse consultation with the Infoplus team.