How to Calculate Warehouse Efficiency
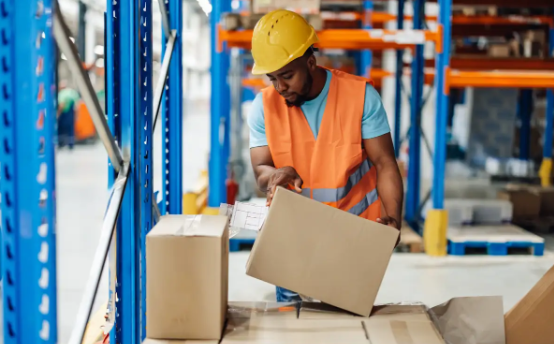
How to Calculate Warehouse Efficiency
Improving warehouse efficiency and management is one of the most productive things you can do for your business. Greater efficiency leads to reduced costs and improved profit, faster order fulfillment times, a better customer experience, lower stress, and a better working environment for your employees. With these wins, it’s easy to see why you should improve warehouse efficiency and consider it a major priority.
Of course, business objectives, customer expectations, and product type can greatly impact how a warehouse operates, so what ends up driving warehouse efficiency and productivity will vary greatly from warehouse to warehouse. This means that every company needs to develop a plan to track, calculate, and measure warehouse efficiency.
Choose the Right Key Performance Indicators
All good plans for calculating and increasing warehouse efficiency start with choosing the right key performance indicators (KPIs). It’s important that you be strategic in selecting your KPIs. If you aren’t measuring the right things, you may not get the data you need to make meaningful efficiency improvements. If you want to explore this topic in greater detail, we already have an article on the topic. But, as a quick summary, a good starting point for KPIs could include the following:
Fulfillment accuracy rate
The fulfillment accuracy rate measures a warehouse’s ability to complete orders without mistakes. This often boils down to ensuring you pick and pack the items your customers ordered to minimize returns and refunds.
Measurement: Successful orders/total orders
On-time shipping
On-time shipping determines how many orders a warehouse prepares for shipping within the designated time limit. Delays can and do occur during shipping due to inefficient warehouse layout, and a low on-time shipping rate can multiply those issues and create an inferior average customer satisfaction score and experience.
Measurement: Orders shipped on time or early/total orders shipped
Cost per order
Cost per order is a vital metric to track, as it’s a strong lead indicator for profitability. Nearly everything in warehouse operations affects this number, including employee turnover, supplier issues, and system outages. Consequently, tracking this number is important as it can serve as an early warning sign of serious issues.
Measurement: Total fulfillment costs/total orders
KPIs Need to Reflect Strategy
This is a short list, and there are many, many more KPIs that you could consider. However, it’s important to remember that KPIs reflect strategic priorities and continuous improvement, not the other way around. The best KPIs take your biggest problems and opportunities into consideration.
For example, if you’re having issues with on-time shipping, you might set KPIs around each stage, from receiving an order until shipping. Or, if you think reducing employee turnover could make a huge difference in the bottom line, you might start tracking employee productivity and satisfaction, safety, and related metrics. And we’ve only looked at a small aspect of warehouse operation so far. Areas like receiving, putaway, and inventory management are critical, and you would measure them with their KPIs.
For a deep dive on choosing the right KPIs for calculating warehouse efficiency, check out our Comprehensive Guide to Warehouse Metrics, KPIs, and Benchmarks.
Benchmark Your Progress Toward an Efficient Warehouse
KPIs alone don’t tell the whole story. In that manner, they’re much like a report card. A report card tells you how you did in each area, but it doesn’t explain why you did well or poorly in those areas. Another way to think about this is that KPIs require context to be useful. A “B” might not be your dream grade, but if the professor mostly gives “C” and “F” grades, you might be performing exceptionally. Consequently, businesses must understand the possible sources of context for their KPIs before they take action.
The first and easiest source of context is your historical sales data and performance. While there can be some randomness from month to month, comparing your last or current month’s KPIs to a three-month rolling average can provide a ton of insight into your current warehouse performance. If the number improves, great! You may need to make changes if it’s static or headed in the wrong direction.
The second way to get context is to compare your performance against similar warehouses. This approach can be tricky, as product types, business expectations, size, available resources, and customer needs often vary from company to company. As a result, these comparisons won’t always be 1:1. Furthermore, it can sometimes be hard to get other warehouses, some of which may be your direct competition, to share their numbers with you. Still, some neutral resources can help. This website contains time standards for pallets, rackables, and binnables based on a guide developed by the United States Navy. Alternatively, you could review studies by the Warehousing Education and Research Council to find the scenarios that most closely match your setup.
Looking at industry standards can help you understand what level of inefficiency is acceptable versus what would be problematic. As a reminder, order fulfillment is a multistep process, and most steps are subject to some level of randomness that may be out of your control. Employees could call in sick, critical equipment or software might break, and your suppliers may occasionally miss their deadlines. While taking steps to reduce the impact of these issues is important, you may never be able to resolve them completely. As a result, it’s not always realistic to target a “perfect” score. Instead, you should target a high but achievable bar.

Leverage Your Insights to Improve Warehouse Efficiency
Once you start measuring your KPIs and putting them in context, the next step is to leverage your insights by designing experiments that target KPI improvements. While it may be tempting to run many different experiments at once, simultaneous experiments may offset and result in no changes, or when things go well or poorly, it may not be clear which change you should attribute them to. In that case, calculating warehouse efficiency measures doesn’t reveal as much as they should.
Ultimately, the changes you make are limited only by your imagination, but they could include automation, workforce training, adopting a new floor layout, or a new pick methodology. Whichever direction you choose, focusing on operational efficiency will ensure that the more data you have available, the more nuanced and effective decisions you’ll be able to make.
Simple Steps, Supported by Automated Solutions
Of course, the more time you spend collecting data, the less you have for critical tasks. That’s why so many businesses work to automate the process to streamline operations. InfoPlus Warehouse Management System Software is designed from the ground up to help businesses get the critical inventory data they need about their warehouse automatically. With custom report scheduling, real-time alerts, and integrations with most major sales software, you can get all the information you need to truly understand your warehouse in a single place.
Book a demo today to find out how utilizing InfoPlus can help your inventory management, get control of your warehouse, and track performance to predict trends and prevent errors.