How to Scale a Warehouse To Dominate Your Industry
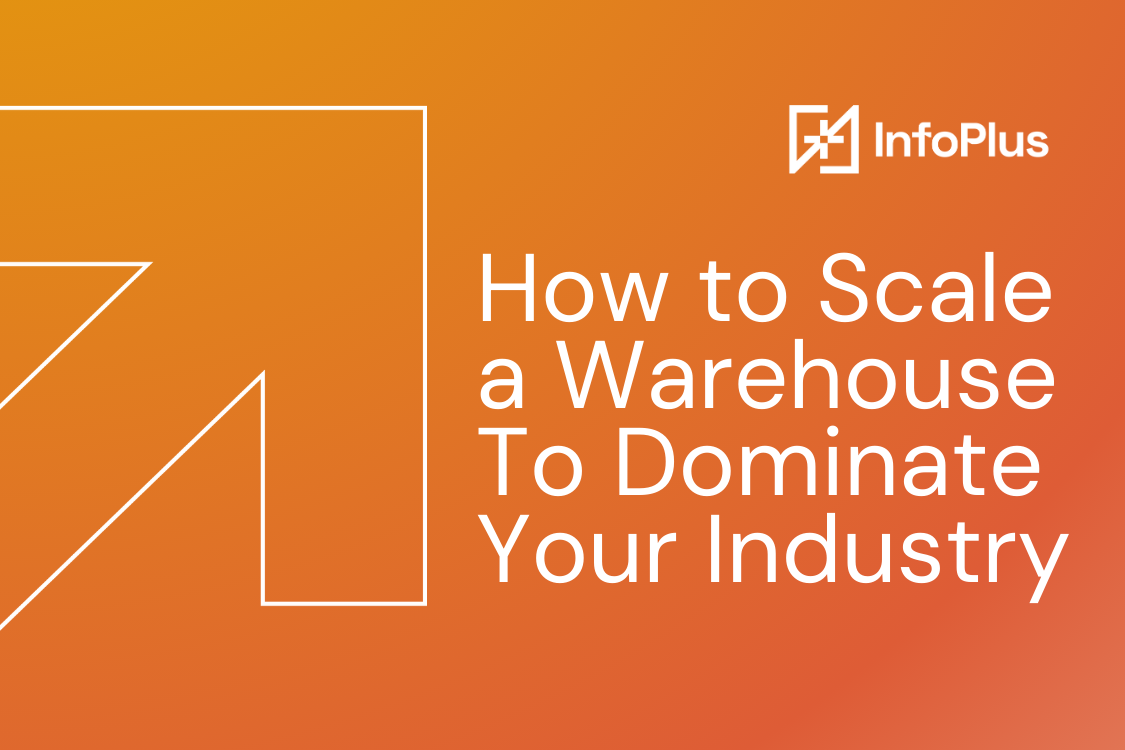
Businesses exist to grow. So it follows that the tools they use to achieve their growth need to evolve with them. Just as a child outgrows shoes, a company will outgrow its tools if those tools don’t grow and scale with the company.
For businesses that are warehouse intensive, this process is a bit more complicated because there are two things that need to scale: The warehouse storage (and shipping) capacity itself, and the WMS/inventory management system used to run it.
So this piece is for those "warehouse intensive" businesses—eCommerce stores, food distributors, wholesalers–who want to scale up operations to take their business to the next level. Specifically, we’ll look at what some of the growing pains are for a warehouse, and how the right tools will address those growing pains and turn them into benefits:
- Inventory Management
- Quality Control
- Warehouse Planning
- Growth and Automation
- Shipping Rate Shopping
- Order Management
Scaling A Warehouse-Intense Business
Warehouses provide the structure through which the business’ lifeblood (products) flow, and they must be managed with care to ensure that your company can scale its operations. Warehouse operations are often viewed as a cost center, but they should be looked at as an opportunity to improve the overall customer experience and increase profits. Accomplished by leveraging a WMS and taking advantage of new processes that provide value throughout the supply chain.
Consistent Visibility of Operations
- Inefficient warehouse layout: Moving inventory around your warehouse costs money. There’s the labor, handling equipment needed, and maybe safety equipment as well. You should calculate these costs in terms of the total number of feet an item moves—for example, a pallet of a given item might cost X cents to move per 10 feet. The costs will inflate if your warehouse is not designed to support your picking and packing processes.
- Inefficient picking/packing processes: You're wasting time and money if your staff is struggling due to a lack of knowledge about the SKUs they need, a disorganized picking system or warehouse layout, or poor implementation of a WMS system that makes it difficult for them to find what they want quickly.
- Poor inventory management: Something is wrong with your setup when an item goes missing from inventory without a sale or if items expire before they’re shipped out.
You can combat these three issues by tracking them carefully and constantly refining your approach so you can keep visibility into operations at all times. If a problem arises, look at the data before deciding how best to address it. Solving these issues as they present themselves will help you scale your warehouse faster.
Optimizing The Warehouse Layout At Every Stage
In order to set your warehouse up to thrive well into the future, it needs to be optimized from the start. You’ll need to consider many factors, such as the type of inventory you're storing, the type of employee who will be responsible for moving that inventory around and maintaining it, and the types of customers that will be buying it.
For example, if you’re just starting out with one or two employees and a small amount of inventory, then all those items can go into one big room where they can access everything. As you grow in size and number of employees, this approach may no longer work—you may need to split up your space again into separate sections or areas based on what items you store there.
But even within each area, there are different approaches depending on whether customers frequently buy those items or not. If some items are rarely sold but need careful handling due to their fragility or value (such as high-end electronics), then only an employee with a key card should have access to this area so that no unauthorized persons enter—and so that people don’t accidentally drop something valuable while moving large quantities out every day!
Many other considerations go into warehouse optimization that can help you avoid common issues in warehouse setups:
- Sub-optimal shipping and receiving areas
- Order-picking paths not optimized
- No separate areas for dead stock, returns, etc.
- Lack of easily recognizable signage and shelf labels
- Treating technology as a toy, not a tool
Investing In Technology
When it comes to warehouse operations, technology is key. It's such an important part of the business that you can't afford not to have technology in place. But before diving into any new systems or software solutions, stop and ask yourself:
- What do I need?
- How much control do I want over my warehouse operations?
- What are my company's goals for its logistics network, and how does technology play into those goals?
- Does my current system allow me to make decisions quickly enough for my needs?
- Are there bottlenecks in the existing system that are slowing down our turnaround time (TAT) or causing delays at peak times?
- Do we need more visibility into what happens within our warehouses—and how long each step takes—so we can optimize processes and improve quality control?
Infoplus’ warehouse management software helps your company analyze these decisions at the start of your company’s growth journey and then seamlessly grows with you as you scale up.
Scaling For Increased Demand
The degree to which business owners have adjusted to rising demand for their goods is what separates those who flourish from those who fail. As they grow, they must build on what they've learned. Data tracking, automation, and integration are the keys.
In order to succeed, a warehouse needs to effectively coordinate its staff, machinery, supply chain carriers, and vendors. Managers often start by searching for answers within these areas when issues arise.
That said, the likelihood is higher that the initial warehouse arrangement and operations itself are the real source of the issue. After all, a poor layout will affect the flow of supplies, machinery, and people throughout the entire area.
A flawed warehouse plan might manifest itself in a number of ways that may ultimately be attributable to other elements, such as underperforming employees, antiquated machinery, or problematic vendors. With the right tools, managers can discover the underlying offender is a poor setup or design of the room by looking a bit closer.
Let Infoplus Help You Scale Your Warehouse
Infoplus: designed by warehouse people for warehouse people to help provide accurate and accessible data to automate processes and make growth simple. If you would like to talk warehouse management software, we’d love to talk with you.