How to Achieve Efficiency with a Single Workflow
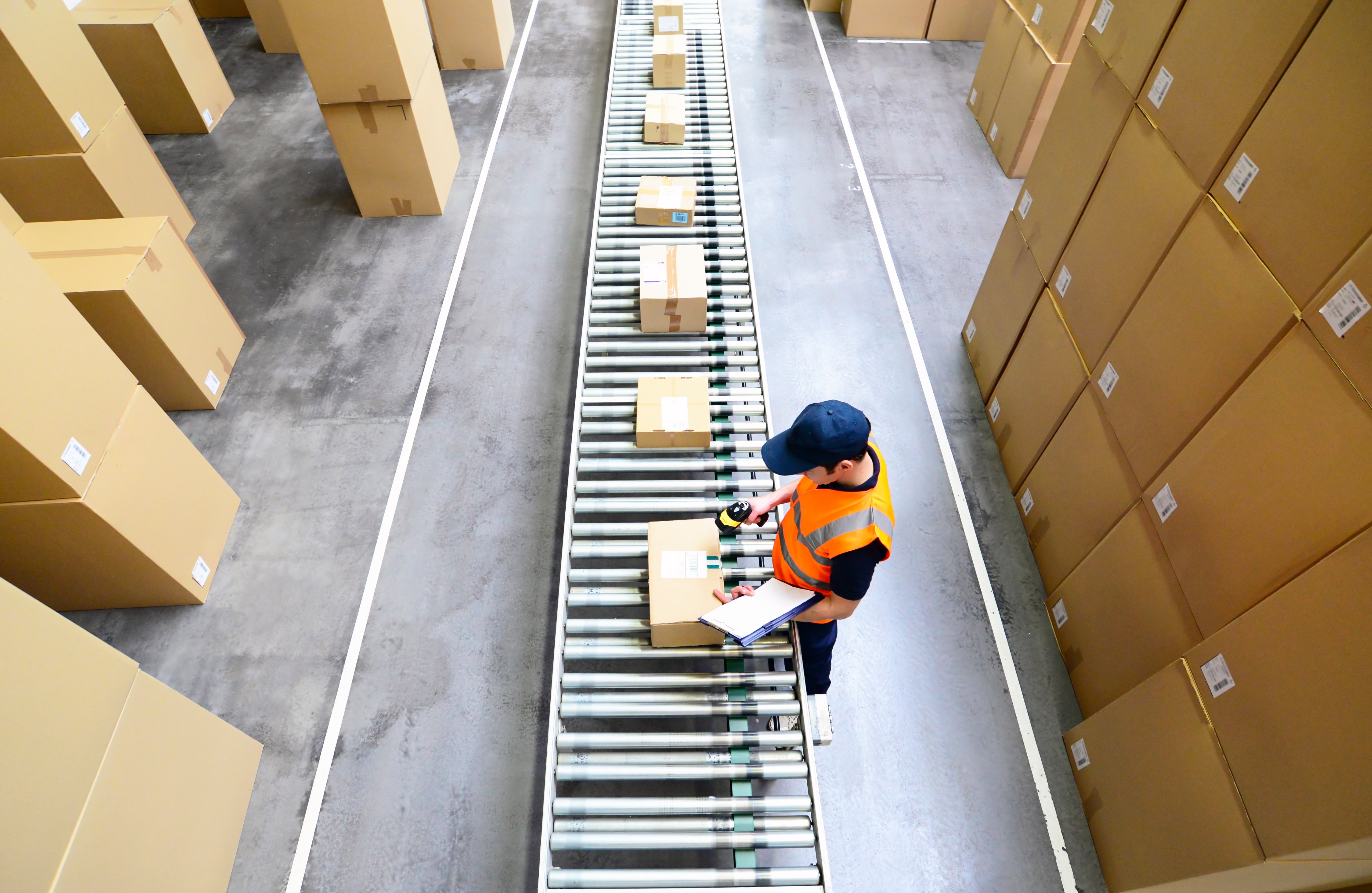
When it comes to software solutions for eCommerce, fulfillment and shipping are often the last things considered. This is unfortunate, as they are often huge sources of errors and inefficiencies. This raises the question: Can a good warehouse management software help?
8 Important Steps for Integration With Shipping
Notice that, in previous posts, we’ve discussed the importance of integrating warehouse management software and fulfillment software with various other parts of your business—for example, ordering channels, accounting software, payment processing, EDI, and more. It’s about time, then, that we highlighted integration with shipping.
That said, integrating inventory management and shipping stations is just one key component in optimizing the workflow for shipping, and it should be understood in that context. Consider the steps that must be performed correctly for shipping to happen quickly and seamlessly:
- Orders must be picked in a fast, efficient, error-free manner.
- If orders are picked in batches, they will need to be brought to a sorting area to separate out individual orders.
- Items must be brought to the packing station and checked to ensure that (1) was done correctly.
- An appropriately sized box must be chosen.
- Items must be packed in the most efficient way possible (to cut down on DIM weight charges) while still guaranteeing their safety.
- A carrier must be chosen to optimize both delivery time and rates, given the customer’s geographic location and shipping preferences.
- Shipping labels must be printed and must accurately reflect the “ship to” address given during ordering.
- A final check must be made to ensure order accuracy and minimize returns.
Needless to say, this can be a very time-intensive process...if each step is done in isolation.Also, you might want to check the eCommerce fulfillment process to get a close view of each step.
An Ideal World: A Single Workflow for Shipping
In an ideal world, the entire process from picking to packing to shipping would be part of a single, well-documented workflow. Each of the above steps would be part of this workflow, of course. In addition, operators and floor managers should consider the following when designing such a workflow:
- Automation. It used to be that workflows were documented on paper—and no one read them. Using an automated software system, next steps can be easily assigned and workers can, with little training, receive clear instructions for their next steps.
- Quality control. The less floor workers have to copy and transfer information by hand, the fewer chances there are for making mistakes. Still, don’t skimp on steps meant to catch errors; include steps for checking item accuracy at each pertinent stage.
- Carrier shopping. Carrier shopping used to be a big pain. Now, automated systems can query several carriers online and pick the best one based on geographic location, DIM weight rates, and more. Removing the manual process and making carrier selection a part of the order process again saves time and allows any worker to complete the task.
- Shipping labels. Most merchants use carrier websites for generating shipping labels. This is not the most efficient way to accomplish this step in the workflow, especially if you need to use multiple carriers or different shipping services. Bringing label creation “in house” as part of the packing process works better.
- A single system. Having separate systems for receiving, optimizing storage, picking, and shipping not only creates extra steps, it invites more errors (see above). A single system can flow data automatically from one process to another and help manage floor workers more efficiently.
- Training. A single workflow, with clearly outlined steps, can reduce the amount of “specialty knowledge” workers need to do their job. This means more freedom when adjusting work schedules, and less time getting new workers “up to speed” on processes.
When our engineers created Infoplus, the goal was not just to create an inventory management system, but to bring all of these aspects of fulfillment into one system to create a single, seamless workflow—including integration with shipping systems. If you would like to see a demonstration of this in action, contact us. We would love to show you how the shipping process can be automated and simplified.