Labor Reduction in the Warehouse - It's About More Than Just Saving Money
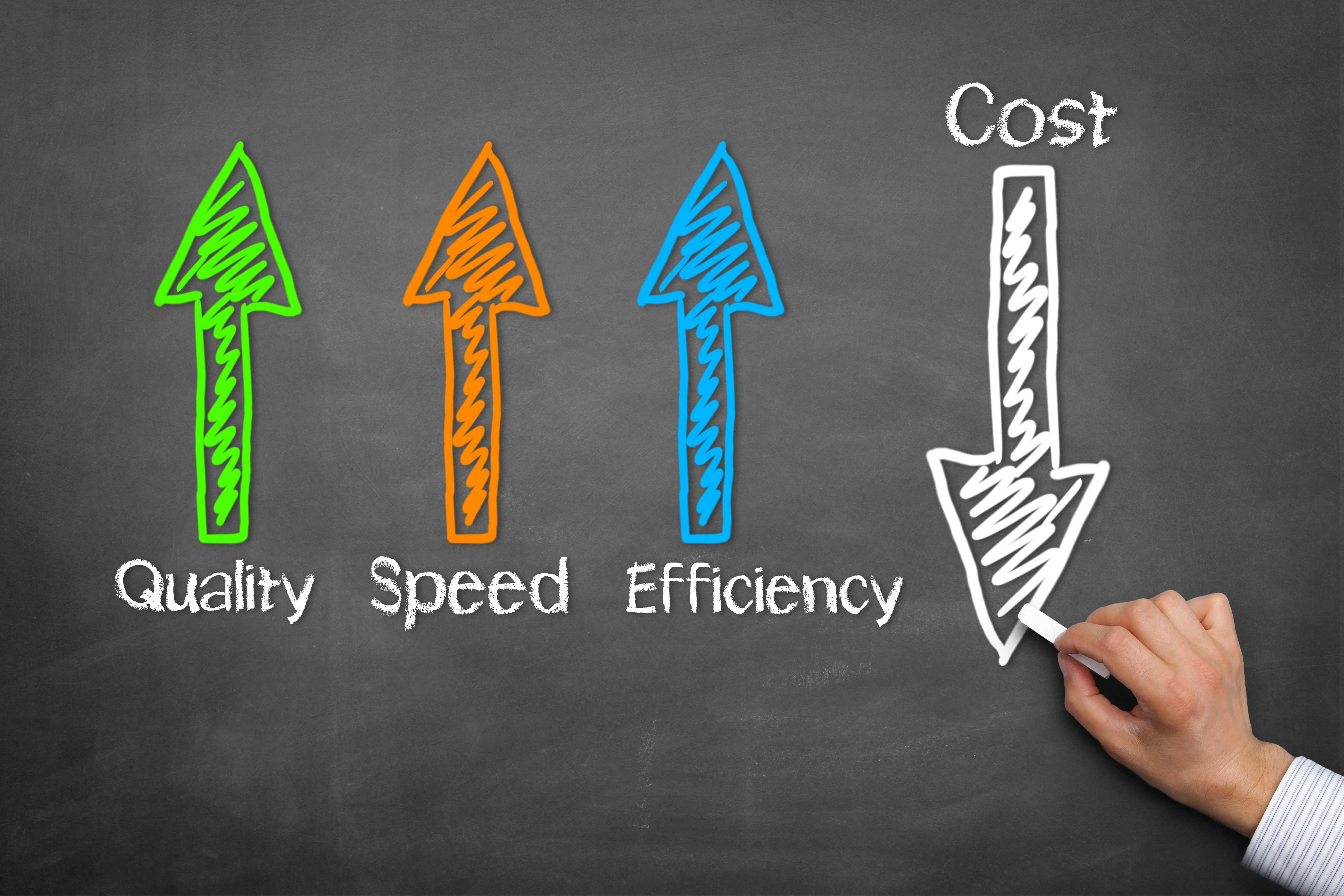
Surprisingly, the task of order picking is, by far, the most costly activity in a typical warehouse fulfillment setting. The only way to reduce this cost while maintaining a functioning operation is to increase the efficiency of picking itself.
Indeed, picking is often a hidden cost center. More than building operation and maintenance, more than inventory management, more than shipping, its the fulfillment activities, including picking, that can erode the bottom line. That’s because they are the most manual-labor intensive activities, with the most room for variance and error.
By one estimate, fulfillment activities account for approximately 40% of the overall labor costs associated with a fulfillment operation.
It’s only natural that businesses continually try to improve their efficiency through better management of man-hours. A well designed operation using a warehouse management software (WMS) should be engineered to radically improve several aspects of fulfillment:
- Achieving same-day processing for competitive advantage against big-name brands
- Eliminating mis-picks
- Increasing pick accuracy
Equally important—maybe most important—among the benefits of a WMS solution is its ability to reduce the labor costs inherent in order picking. This is accomplished through optimizing your warehouse route, setting up “layout by order,” and utilizing wave picking.
Warehouse Route Optimization
Route optimization is one straightforward way of making your workforce more efficient. For example, one warehouse we’ve worked with was in the habit of picking orders sequentially, one item at a time. This meant that, if two orders had similar items in them, there would be two separate trips to the same area of the warehouse!
Optimizing the pick route is one way of reducing the redundancy here. Essentially, a software can find the most optimal route between stops in the warehouse, cutting down the total distance travelled. When paired with the appropriate layout and “batch” wave picking methodology, the labor savings can be quite significant.
Layout By Order
Layout of your operation is more important than most merchants think. A WMS helps you more easily target your most commonly picked items, leading to a more efficient floor/inventory design, which in turn creates more practical warehouse route(s).
Essentially, users can create a “warehouse within a warehouse” by grouping together the SKUs that make up the majority of your orders, or that are frequently ordered together. This, along with route optimization, cuts down on travel time for pickers.
Couple these things with a software’s ability to allow you to place picked items into a bin representing an order, and a well run warehouse can cut down on the time and labor associated with sorting and packing orders. The orders can show up at the packing station presorted needing only to verify, or simply transfer into a shipping carton.
Wave Picking
Wave picking, a type of short-interval scheduling for order picking, is used to help organize the daily flow of work of a warehouse. It allows supervisors to assign groups of orders into short intervals called “waves” to group and anticipate the flow for the day, consistent with the order departure plan and available labor.
Using wave picking, a well configured WMS software can release waves to a warehouse sequentially throughout any given day, allowing managers to coordinate the several parallel and sequential activities required to complete daily work. This helps minimize the variation of workload in each work function by wave. The wave data may include the workload (i.e., order lines, cases, value-added services) by order or function (i.e., case picking, repack picking, pallet movement, pick position replenishment, packing) for the purpose of providing management the information to calculate staff requirements.
Yes, reducing labor costs in and of itself is important. But even more so when you realize that a more efficient warehouse process naturally leads to same-day processing, fewer mis-picks and high pick accuracy. Which always leads to greater customer satisfaction.
If you are interested in finding out how a WMS could potentially help you cut down on labor and improve accuracy and efficiency visit Infoplus for a free consultation at www.infopluscommerce.com