Errors in Warehouse Fulfillment? Here’s What Might Be Wrong
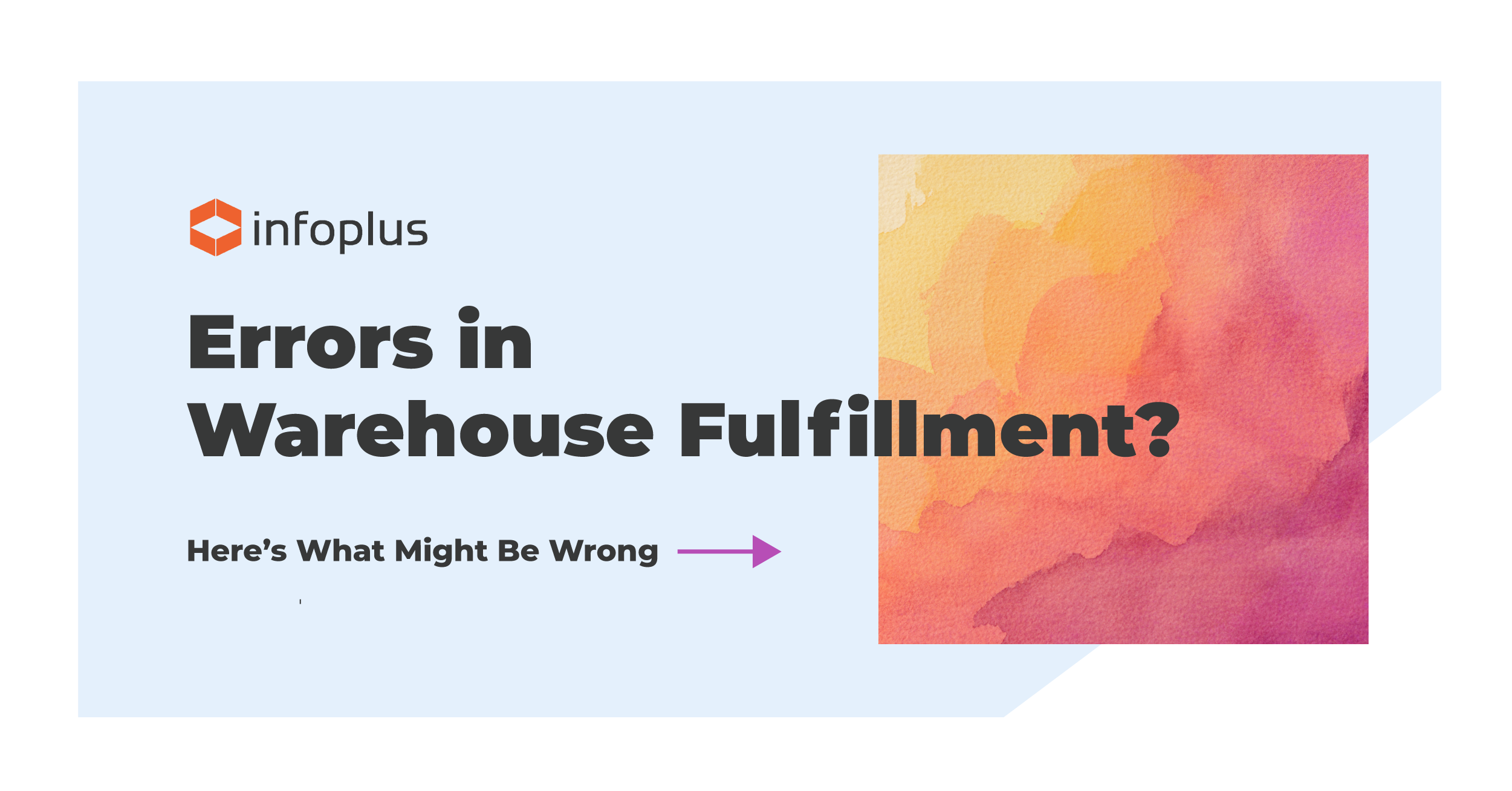
The inability to fulfill orders means an inability to fulfill customer expectations. Unhappy customers won’t be a problem for long—they’ll just take their business elsewhere. Mistakes that drive customers to a competitor can spread like a virus. Managers need to recognize the symptoms of warehouse fulfillment mistakes, diagnose the problem, and apply the appropriate treatment.
Expecting perfect performance 100% of the time is unrealistic. Warehouse managers acknowledge that there will be errors and know what they feel is an “acceptable” level. But the goal is always to push that needle as close to zero as possible. Before you can go about improving performance, the first step is to figure out what you’re doing wrong.
Recognizing the Symptoms of Fulfillment Mistakes
Mistakes in warehouse fulfillment show up in a few distinct ways. If ignored, these things have the ability to trigger problems in other areas in the warehouse, undermine operations, and ultimately hurt the bottom line.
The appearance of any of these symptoms is an indicator that there are fulfillment mistakes that must be addressed.
An Overabundance of Returns
Sure, merchandise might be sent back because the customer changed their mind. But it’s often because something went wrong at the warehouse or distribution center:
- The wrong items can ship
- Orders might be incomplete
- Products can arrive damaged
- In some cases, the online description or representation might not be accurate.
Whatever the cause, returns mean refunds or replacements. They also require a system to manage them that involves receiving, recording, and either disposing of, reshelving, or returning the returned items to the vendor.
Customer Complaints
An uptick in complaints or negative online reviews can be a symptom of a warehouse fulfillment problem. Managers need to pay attention to the type of complaints to find the source of the problem. Receiving damaged goods or late deliveries are signs of fulfillment mistakes. Comments about unhelpful customer service reps or poor product descriptions on the eCommerce site, on the other hand, are problems to be solved by HR or the sales team in charge of the website.
A Backlog of Orders
Mistakes in warehouse fulfillment often show up as an inability of staff to keep up with orders. A number of different problems can cause a backlog, including an inefficient layout, supply chain problems, or not anticipating seasonal spikes. The backlog is the first clue there is a problem. Deciding the source and what to do about it will take a bit of research.
A Clogged Shipping Area
Fulfillment isn’t complete until orders leave the warehouse. When things start to stack up waiting to go out the door it’s a sure sign that there are mistakes in warehouse fulfillment. The worst part about it is that it will start a domino effect: Shipments arrive late. Products become damaged or spoiled. This leads to returns, complaints, and eventually lost revenue and customers.
What Might Be Wrong and How to Fix It
These symptoms and the underlying issues that cause them rarely exist all by themselves. Instead, they are often intertwined, one causing or contributing to another. Likewise, one solution might cure several ailments, or a few different solutions might, in combination, fix the fulfillment mistake. Let’s look at what might be wrong with your warehouse fulfillment and what to do about it.
Fulfillment Error #1: Bad Layout
As we’ve discussed in many of our articles (check out our Warehouse Set-Up 101 Series on optimizing small, medium, and large warehouses), a warehouse’s layout is key to efficient operations. An organized floor plan includes proper slotting and rack labelling, as well as clear pick paths. Even making sure it’s well lit and clean can make a difference.
Many picking errors are due to improper labelling, sloppy storage, or pickers that feel “rushed” to fulfill orders—and often, it’s a combination of these. Paying attention to the layout of the space can cut down on picking errors or incomplete orders that result in returns and complaints. It can also increase productivity, with faster order fulfillment, ensuring that employees keep pace with orders and get them out the door in a timely manner.
Fulfillment Error #2: Poor Inventory Management
Breaking the 3 Rules of Inventory Management will cause a host of mistakes in warehouse fulfillment. Not stocking enough of a product will create backorders—and unhappy customers. Overstocking can clog up aisles, interrupting the flow of pickers (not to mention the unnecessary cost of ordering too much).
Fulfillment Error #3: Not Automating
Eliminating human error by automating wherever possible will get a warehouse closer to that perfect performance goal. Automated solutions allow for faster, safer, more accurate order fulfillment.
There are many ways to automate a warehouse at every scale. Having machines and software take on various tasks can eliminate a lot of man-made mistakes. For example, one of the most common and most helpful automated solutions for better order fulfillment is bar code scanning. Barcoding can automate inventory receiving, storage, picking, and quality control as it tracks products on their route through the fulfillment process. Other innovations like voice picking software, which can guide pickers to the proper location, can completely change fulfillment accuracy for the better.
Fulfillment Error #4: Inadequate Quality Control
Quality control is important in many areas of warehouse operations. It can mean checking that the right amount of items arrive at a warehouse in good shape. It can also mean checking that the right things end up in a box bound for a customer. Managers must determine where in the fulfillment process inspections make the most sense, based on the problems, or potential problems.
The following quality control checks can help to ferret out mistakes:
- QC for damaged products arriving in the receiving area could uncover a vendor problem.
- QC while picking could show that the storage location isn’t keeping products safe from harm.
- QC while packing will show that the items and quantities match the orders and may dictate the best packing materials to protect fragile items.
- QC at shipping ensures that the correct things left the building for the customer in good shape—if the customer receives damaged goods, it is probably a carrier issue.
Fulfillment Error #5: Ignoring KPIs
Warehouse Management Software is capable of providing valuable analytics down to the most minute detail. These key performance indicators, particularly those that deal with the fulfillment process are a goldmine of information. Data such as increased order lead time, or a decrease in orders picked per hour or percentage on-time delivery indicate where to look for problems in warehouse fulfillment.
Warehouses need WMS software that can be customized to measure the data that is most meaningful for the company and its product. When the reports giving the appropriate KPI information are available, warehouse managers have the tools they need to correct any mistakes.
Fulfillment Error #6: Decisions Aren’t Data-Driven
The usefulness of KPI data goes beyond finding mistakes that need to be fixed. It can also be the basis by which managers make many decisions in the warehouse. Rather than going by their gut, they have clear analytics that inform the choices they need to make to keep order fulfillment on track.
For example, automatic order alerts can be set to place orders as soon as products fall below a certain level. Using the data to drive decisions reduces the chances that employees will miscount inventory, wait too long to order, or forget to do it entirely.
Also, real-time data that tracks carriers’ cost, availability, speed, and accuracy can be set up to automatically initiate a shipment with the shipping company that’s most appropriate. It can also measure past performance to predict if a late delivery is a one-time error, a problem that happens during certain circumstances like a storm, or a worsening trend.
Fulfillment Error #7: Failure to Integrate
Integration goes hand-in-hand with automation to ensure smooth order fulfillment. It means that all of the machines, software, and people are working together to get things done, reducing miscommunication or duplication of tasks.
The automated ordering mentioned in Fulfillment Error #6 is an example. In this case, pickers’ barcode scanners keep track of what is taken off the shelves. This is part of the Inventory Management System that provides real-time data about what’s left. When a preset number is reached, the purchasing department is alerted and they can place the order.
Or, when a repeat customer places an order and indicates a change of address, several departments can be notified at once. The accounting department can change billing information, the marketing department can redirect catalogs to the new address, and most importantly, the correct address will end up on the shipping label for the current order. Without integration, each department needs to be informed of the change and re-key the information into its own part of the software. It’s easy to see the potential for mistakes in warehouse fulfillment.
(For more examples of warehouse software integrations and their benefits, see our white paper “5 Exciting Ways Software Integration is Revolutionizing Logistics.”)
Improving Warehouse Fulfillment Means Finding and Fixing Mistakes
No warehouse can be perfect all the time. Mistakes are going to happen. But managers don’t need to accept that “that’s just the way things are.” There are solutions to the problems that get in the way of successful order fulfillment. Proper diagnosis of what’s ailing operations comes first. Then, an appropriate treatment plan can be put into action.