6 Things That Will Sabotage a Shipping Area Layout
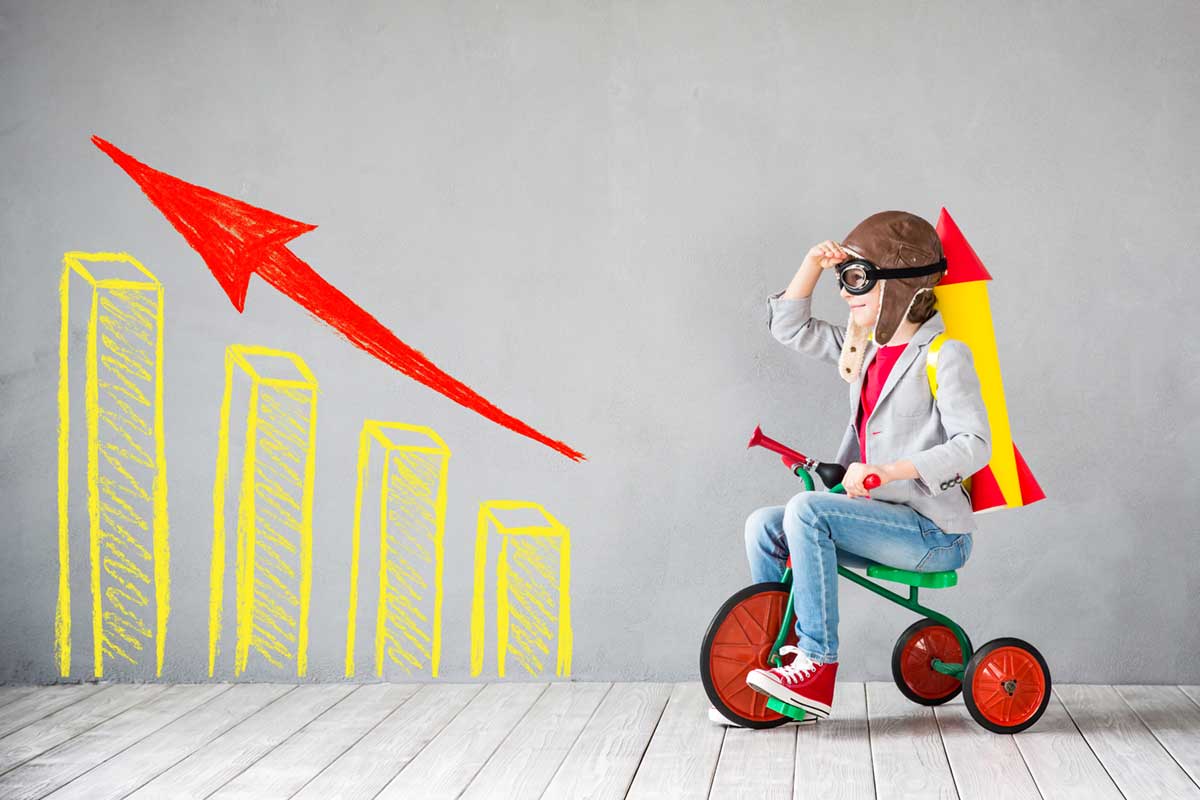
Shipping Area Layout Workflow
In a typical warehouse packing and shipping department, several things need to happen. First, items are packed for shipping. This step might include bundling items together, wrapping products in protective materials, packaging them in boxes, bags, or crates, and sealing them.
Next is quality control. This will involve inspecting orders to make sure they are undamaged. Someone must also verify that the order is complete and correct, and matches corresponding documentation.
After that, outgoing orders are moved to a staging area where they are sorted and grouped together. Pallet loading comes next. Their final destination is near the loading dock or exit door, to await loading onto trucks that will deliver them out into the marketplace.
To make all these steps come together effectively, packing and shipping areas must have well-thought-out processes, proper equipment, and clear employee procedures. Mistakes in this area can be costly. Simply put, if goods don’t make it into customers’ hands, you don’t get paid. You should know critical factors that can have negative impact on overall efficiency. Here are six ways shipping area layouts can fall short—and ways to avoid these missteps while designing warehouse and storage layouts.
1. Flawed Warehouse Layout Design
Getting orders out of your warehouse door to customers quickly and accurately relies on a chain of events starting way back in the receiving area. Every step taken in the warehouse must be optimized for efficiency. Delays “upstream” in a warehouse will slow the arrival of products in the packing area and customers will be unhappy if they don’t receive their orders on time.
If operations elsewhere in the warehouse consistently interfere with the steady flow of products into the packing area, it’s time to reconsider the overall warehouse layout design and floor plan. Is the receiving department documenting items and putting them in the correct location? Are storage areas organized so pickers can find things? Are workers moving along the most efficient pick paths? Do you have the right material handling equipment to move products quickly and safely?
Warehouse layout and operations must maintain a consistent flow. If not, the packing and shipping areas will be victims of the domino effect.
2. Lack of Quality Control
Poor quality control standards can lead to incomplete or incorrect orders or shipping damaged goods. All of these will lead to customer complaints and lost sales.
To combat this problem, there must be clear quality control procedures in place. Employees must make sure that the products are packaged in good shape, and that they match shipping documents.
Workers will follow specific guidelines appropriate for the items being packed. For example, protective supplies like craft paper, bubble wrap, packing peanuts, or padded envelopes will avoid breakage in transit. Many businesses also have strict rules about how many and what types of items can be packed together.
The other aspect of quality control is checking that the orders are complete and accurate. The items going into the packing container are compared to the order form or packing slip. This can happen manually with a paper checklist or using barcode labels and scanners.
3. Poor Packing Station Design
The design of individual packing stations plays a significant part in ensuring that materials leave the warehouse intact. Workers must have the right tools to prepare things for shipment.
Workspace:
Packing stations should start with a worktop that is big enough for the task at hand. Packaging large boxes or assembling batch orders might require a long countertop instead of a small table.
Worktops and stools or chairs should be ergonomic. Ideally, they should be adjustable to accommodate employees of any stature.
Managers should decide how many packing stations to set up based on the needs at the warehouse’s busiest time. They must be capable of filling orders when working at full capacity.
Materials:
Each packing station needs to have the necessary packing supplies at the ready. These will include the protective materials needed to avoid product damage, as well as an assortment of boxes, bags, envelopes, fasteners, tape, and tape dispensers.
Shelves above, below, or behind the worktop will keep supplies within easy reach of the packer so they do not need to walk to another area of the warehouse to get them. Avoid making them lift heavy items off the floor or down from high shelves.
4. Unclear Documentation
Getting orders right relies on good documentation. Order forms, pick lists, packing slips, bills of lading, invoices, or any combination might be used in the shipping area.
Automating the documentation process with barcode scanners will increase accuracy and productivity. Mistakes, like transposing numbers, illegible handwriting, or losing paperwork, can be reduced if not eliminated.
Many times, a documentation and barcoding method is dictated by the customer. Big-box stores often have strict requirements. For example, they need barcode labels affixed to all four corners of a pallet. Packing slips or bills of lading might be placed inside each box, affixed to the outside, or to the outside of the pallet, depending on the customer’s wishes.
Implementing an automated documentation process will require some additional equipment in the packing and shipping area. The layout will need to include computer monitors, keyboards, and mice, barcode scanners, labels, and printers. This might mean separate desks, tables, or workstations, or the integration of this equipment into the packing stations.
The packing and shipping area should have dedicated printers for their tasks. Walking to another part of the warehouse to pick up printouts wastes valuable time. Likewise, they should not need to share their printer with other departments. The more people using one printer, the greater the chance of bottlenecks and equipment malfunctions.
5. Unnecessary Steps
Managers should always be on the lookout for warehouse tasks that can be combined or eliminated to make the process more efficient. Here are some ways to streamline operations in the packing and shipping area.
Packaging Area Layout and Shipping Area Layout
Reducing the number of times an item is touched and the distance traveled is always a priority. Your warehouse floor design should be logical and mapped out to avoid backtracking, cross-traffic, and bottlenecks for workers and equipment.
Choosing Box Size
Some companies limit the variety of boxes they use for packing. It is sometimes more cost-effective to ship small items in a larger box filled with lightweight packing material than to stock boxes in every conceivable size to fit each product.
Boxes in a few common sizes and shapes are easier to stack uniformly on pallets for shipping. It also takes a packer less time to grab a box from one stack than to search for a different size for every order.
Automation
Using barcoding for documentation procedures is just one step-saving way that a shipping area can benefit from automation:
Weighing and Measuring:
Automated scales and dimension measuring equipment can be integrated into the workflow of the packing and shipping areas. This gives accurate weight and measurements that will aid in pallet loading.
Moving Materials:
Equipment like automated hand trucks, forklifts, or conveyors will save steps when moving products through the packing and shipping area.
Package Handling:
Time can be saved by automating tasks related to preparing pallets for shipping. Automated pallet stackers, pallet nailers, and plastic wrapping machines are some examples.
Staging Area vs. Direct to Pallet
Let’s say a warehouse ships items via UPS, FedEx, and USPS. Boxes go from the packing stations to a staging area. There the boxes are sorted according to the carrier and stacked separately, waiting to be loaded onto pallets. A more efficient procedure might be to stack packed boxes directly on designated pallets. Once full, the entire pallet can be picked up by the carrier.
One method is not better or worse than the other. And some shipping areas might do both. The decision will depend on what works for the specific company.
6. Clutter
A surefire way to sabotage the efficiency of a packing area and shipping area layout is to allow the space to become cluttered. The moment a workspace becomes messy, mistakes will start to occur.
In a disorganized environment, it is easier to send the wrong products to the wrong customers. Incomplete orders might go out. Or damaged goods might find their way into outgoing boxes.
And if a warehouse isn’t just disorganized, but dirty too, bad things will happen. Industries dealing with food, pharmaceuticals, or medical products, especially can’t risk contamination.
Combatting clutter starts with having everything in its designated place. It is a matter of having effective processes in place for your warehouse design layout. This consists of clear procedures that are communicated to employees and a layout that is optimized for efficiency.