Stop Relying on Manual Data Entry
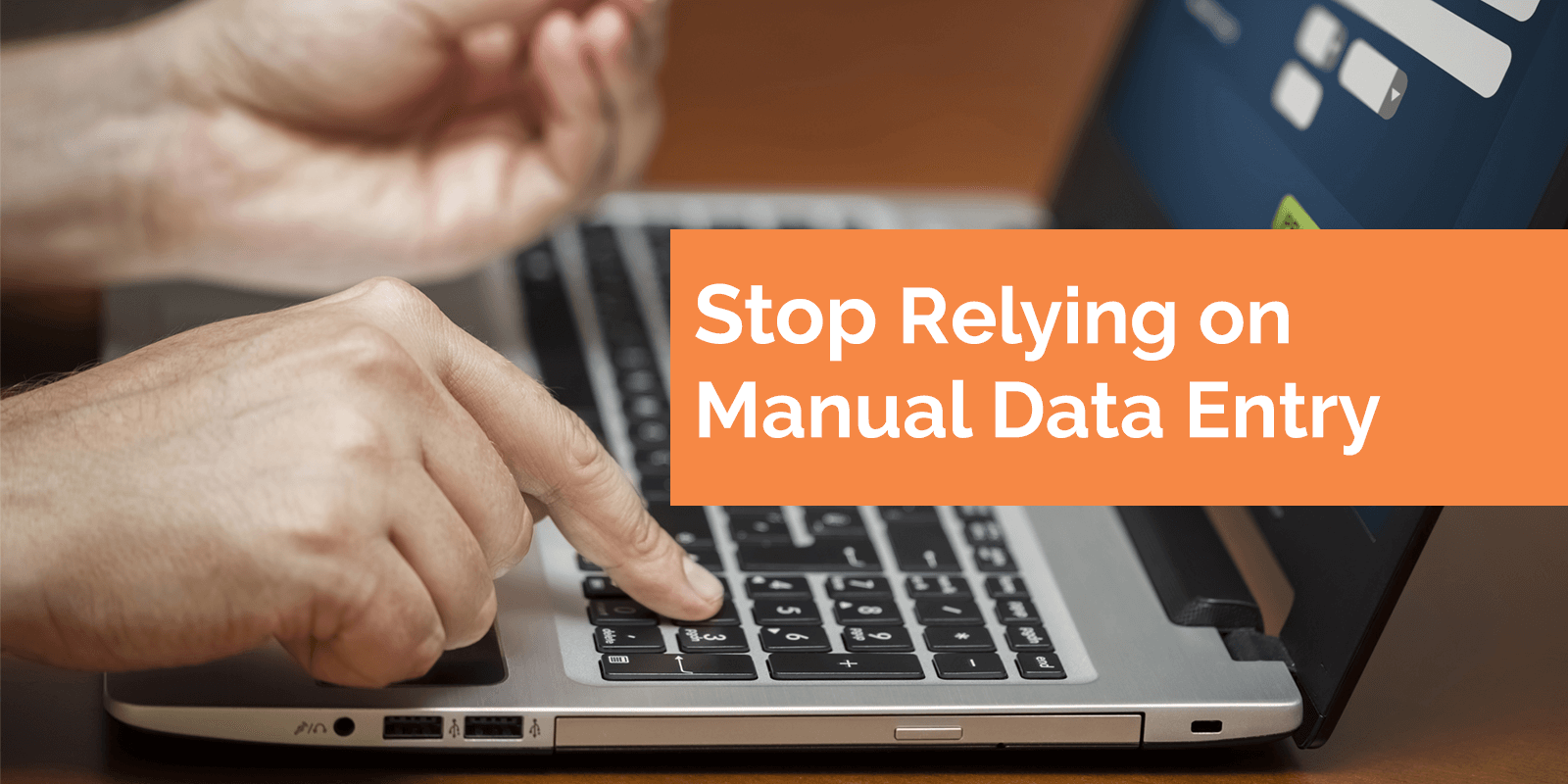
The other day, a colleague (who will go unnamed, of course) mentioned that the warehouse manager still entered product details manually when items were received, and packers would have to recode this information into the shipping system when it came time to ship.
They were almost proud of their low-tech operation. But it was the kind of pride that could stand only because they ignored all the customer complaints.
Some organizations insist that their inventory management need not go digital. In a way, they’re right: Inventory and warehousing practices existed before computers, and could continue to do so, if necessary.
Then again, employees could ride to work on horses, too. Sure, an employee on horseback would get from A to B...just don’t try it on the highway, and don’t expect to win any races.
Likewise, facilities that have not gone digital are at a severe disadvantage these days, compared to the competition. Information for each product and order either has to be written by hand or entered manually into a computer system—or else, not recorded at all. Even when computers are used, manual data entry means that the same information often has to be entered and re-entered into different systems (for example, inventory, then a shipping station, then accounting software, and so on).
Is this just a matter of needing a little additional elbow grease, then? Not at all. Manual data entry isn’t just slower; it is a step-change that limits the kinds of activities needed to stay competitive. By moving from manual data entry to automatic data updates:
- Human error is reduced. Logistics is a game with little tolerance for error. Customers expect to get the right items in a timely manner, no matter what the product. Quantities are precise. SKUs have specific locations and destinations. And so on. Manual data entry makes the process longer and more laborious, and the longer and more laborious a process, the more likely an error (or several) will occur. Items might not be appropriately registered in the warehouse or could get misplaced. Reports might be inaccurate. Shipping labels can be misapplied, sending the wrong packages to the wrong parts of the country. Only when there is a single, continuous workflow with the appropriate checks can you contain and mitigate such errors.
- You’ll know when to reorder. Customer expectations in regard to item availability and shipping have been very much shaped by Amazon, Zappos, and other online giants. Getting into a backorder situation is no longer an option. Manual data entry is often too slow to prevent this, especially with high-velocity items. With an integrated inventory management system, appropriate parties can receive alerts when stock is running low, thereby triggering an order. It can also keep track of your products’ availability and calculate how much product you need to reorder to minimize wait time while preserving cash flow.
- Reporting becomes more extensive, useful, and fast. With older systems, reports were always a backward-looking snapshot of what had already happened. Data were aggregated over the course of a month or more, and reports were received no more frequently than that. Manual data entry was (and is) one culprit: It is a time-consuming exercise that leaves little room for activities such as reading, analyzing reports, strategizing, and planning for growth. More time is spent on data hygiene than actual decision-making using that data. Having data that are automatically entered into the correct reports, in real time, allows up-to-date, accurate reports with no additional labor or time. This kind of reporting can also identify small ways to cut costs and boost margins. Many of these small improvements might be too small to justify a large labor expense but are perfect for an automated system.
- Problems are found (and can be fixed) right away. Manual data entry and infrequent reporting also mean that problems take time to detect. Problems that are not detected quickly can quietly fester, becoming larger and quickly spawning new problems. For example, a shopping cart app that is not updated to reflect current stock levels can create a host of backorders. A spike in sales might fail to trigger a reorder. Or a customer’s change of address can result in mis-shipped items, leading to some bad online reviews. On the other hand, automatic data integration allows for reports daily, or even more frequently. Problems are caught sooner and handled as needed.
- Everyone, large and small, is catching on. It used to be the case that only larger operations could afford the kinds of enterprise systems that integrated and automated this type of data collection. That is no longer true today. Even small eCommerce outfits are taking advantage of software solutions that manage all of the “back end” elements to logistics and shipping. This has led to faster order turnaround, better customer service, and more agile businesses.
What’s the Alternative to Manual Data Entry?
Manual data entry is the worst option for keeping a warehouse or inventory database, right after “no data entry at all.” So what are better alternatives?
A slightly better alternative is to find ways to integrate various systems across the organization. For example, is there a way to integrate your WMS with your shipping stations? With the organization’s accounting software? (Even here, the type of integration matters. Integrating your standard ERP will be tougher than a software solution using APIs, for example.)
Even better would be finding a system that natively incorporates these functions from the start. Instead of piecing together software solutions and hoping they can “play well” together, a good warehouse leadership team will invest in a system that already has inventory, labor management, receiving, and shipping capabilities, and that is compatible with most shopping cart and accounting software “out of the box.”
The profusion of technology in logistics should not make us nostalgic for the days when a single inventory manager could keep all those order details and stock locations in his head. As scary and confusing as technology can be, not relying on it is even more frightening. Until humans can match the speed and precision of machines, manual logistics procedures will always be at risk.