How Am I Underutilizing My Warehouse Layout? Common Oversights and How to Optimize Them
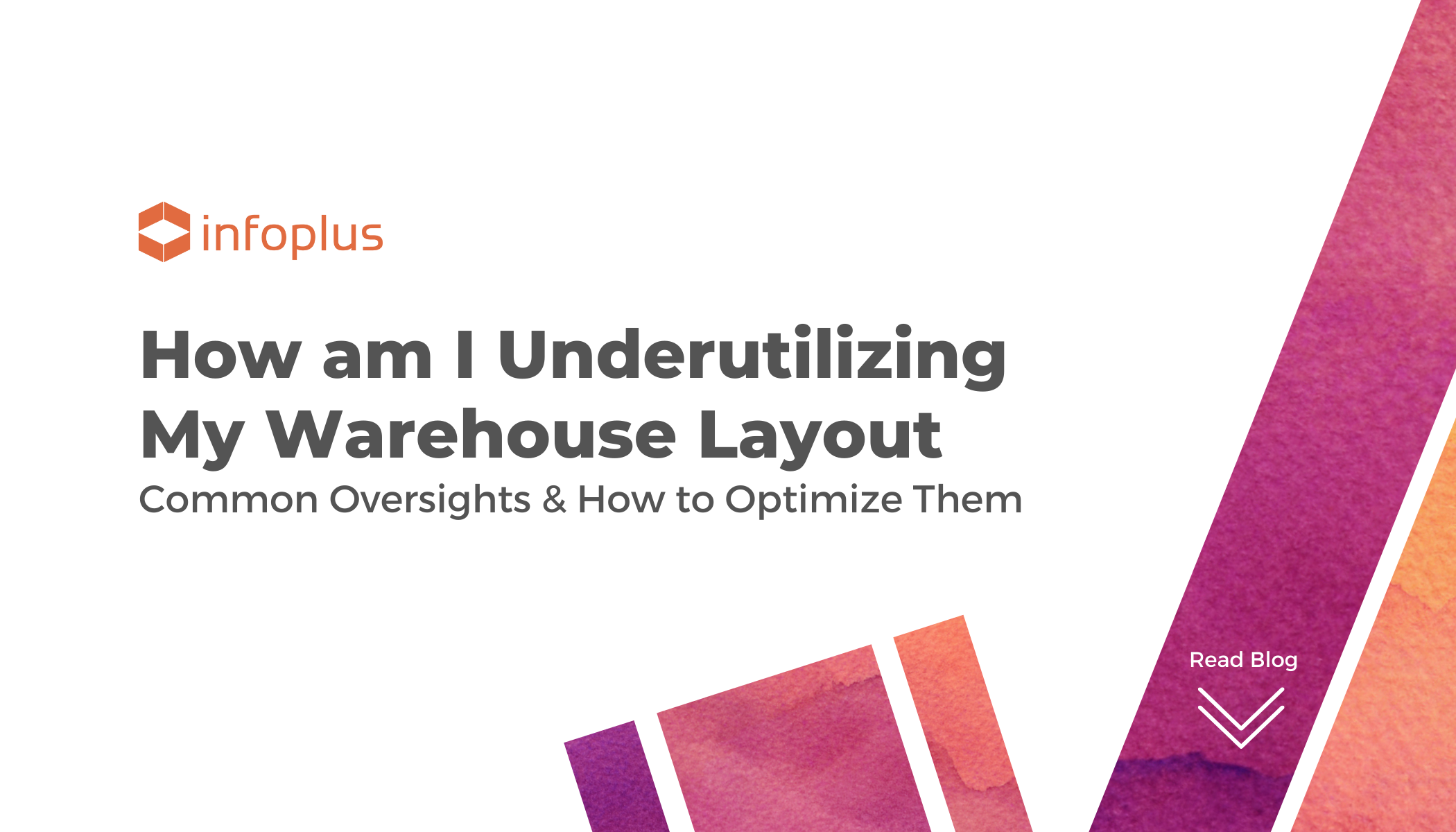
An optimized warehouse layout requires more than just good organization. If you’re experiencing inefficiencies, you could be underutilizing important parts of your warehouse.
In fact, three of the most common oversights that decrease productivity in a warehouse are:
- Disorganized inventory
- Inefficient pick paths
- Outdated manual processes
Learn why these warehouse elements aren’t often optimized, why underutilizing them can cause major bottlenecks, and how you can address these oversights to increase efficiency among you and your staff.
How Am I Underutilizing Parts of My Warehouse Layout?
If you notice a dip in your projected ship-outs or backlogged orders, you might need to make some adjustments. First, ask yourself if your warehouse layout aligns with best practices.
Warehouses experiencing underutilized areas usually see problems with:
- Unorganized pick paths and picking methods
- Unorganized inventory
Without best practices for these warehouse functions, your employees may just be doing what’s convenient, as opposed to efficient, or changing their methods from day to day.
How Should You Organize Inventory?
If you’re in the habit of putting your inventory wherever it fits, your warehouse layout can quickly become disorganized.
Enter your slotting methodology.
There are two kinds of slotting: Micro and macro slotting.
- Macro slotting refers to optimizing the layout of your warehouse and its inventory.
- Micro slotting is the way individual items or pallets are put in specific zones and shelves in your warehouse.
Inventory slotting is more than keeping a map of where everything belongs. Gathering data on your SKUs needs to be taken into consideration when thinking about slotting best practices.
Without best practices around warehouse slotting, which is where and how you stock your inventory, pick paths can’t exist and your employees will be digging through units to fulfill orders or waste unnecessary time looking for hidden SKUs.
To create the ideal micro slotting method, it’s important to understand:
- Item quantity description for picking (single unit, case, full pallet, etc.)
- Item storage type (pallet, shelf, carton, etc.)
- Cube size and weight
- Seasonal fluctuation
- Special storage requirements
- Item velocity
- Items commonly shipped together
Once you can identify what items should go where based on relevant data, you’re ready to slot your inventory.
Depending on the size of your warehouse, efficient slotting can save your pickers time on their paths and help them fulfill orders faster. When you nail inventory organization, it’s estimated you can save between 40-60% of worker time during warehouse operations.
Some other benefits of utilizing efficient slotting include:
- Increasing visibility and reducing error
- Minimizing item damage
- Removing bottlenecks
- Reducing travel time
- Freeing up space
By utilizing slotting best practices, you can keep slow-moving inventory out of the way while keeping fast-moving SKUs flying off the shelves. With your inventory in place, you’re able to put efficient pick paths into effect to save your warehouse time and money.
What is a Pick Path?
To implement efficient pick path methods, it’s important to educate yourself and your employees on what a pick path is. Simply put, a pick path refers to the order in which picking teams pull SKUs off the shelf to fulfill orders.
Employees typically pull multiple SKUs simultaneously for multiple orders to decrease the number of times they have to walk back and forth in the warehouse.
As an example: Suppose your warehouse receives 10 orders at a time. Instead of your employee or picker taking 10 separate trips to retrieve inventory to be wrapped up for delivery, they can follow a pick path and gather each SKU in one sweep, saving time in the process.
The three most common picking methods are wave picking, batch picking, and zone picking.
Wave Picking
Wave picking focuses on saving the number of steps pickers take to fulfill an order. As you walk through your warehouse, you’ll take no step twice. Pickers will fulfill individual line items by walking down each aisle one way, then the other way, so they don't have to stop at various points to cross the aisle.
Like a wave, you follow the current of the direction you’re heading, crash, pivot at the end of the aisle (crash like a wave), and begin a new wave cycle. Depending on the aisle width in your warehouse, you may utilize equipment to make this process even more efficient.
*TIP: Consider the width of your aisles when you think about pick paths and your choice of equipment. If you have room for two lanes, that’s ideal, but if you’re operating in a single lane pick path, communicate with other pickers to prevent any bottlenecks.
Batch Picking
Batch picking takes the wave picking method a step further so picking teams can fulfill multiple orders at once.
Batch picking can significantly cut down order fulfillment time, especially for large warehouses with a plethora of orders. Depending on your warehouse, there are two ways to sort orders for batch picking.
The first way is called picking by SKU. Pick everything in one wave then sort each order at a staging area before packaging.
The second is called picking by order. Alternatively, you can place marked bins on your picker’s cart so they can sort the orders as they go and send them straight to packaging. This solution eliminates the need for a staging area and potentially saves time if your picker is precise.
Zone Picking
Zone picking saves individual pickers from scouring your entire warehouse for individual line items in an order. Pickers are assigned a “zone” or aisles, and as you receive orders, each picker delivers the line items in their “zone” to a staging area before moving to packaging.
Using this method, each picker can be an expert in one area of the warehouse and develop ways to pick their zone the fastest.
Each of these picking methods can be used together to create the most efficient system for your warehouse.
*Wave picking and other methods require a WMS that can coordinate and time the release of waves to the warehouse throughout a given time period.
How to Gather Data to Optimize Warehouse Layout
Full warehouse utilization is difficult to do, especially if you’re attempting to take it on manually. Whether you’re looking to optimize your pick paths or you need to start with an efficient slotting method for inventory, using a robust warehouse management system (WMS) can help automate manual processes.
The right WMS can give you a virtual overview of your warehouse, providing you with visibility to where everything is stored so you can adopt the most efficient pick path practices. Realizing your warehouse oversights can be overwhelming, let a WMS help you reconcile inefficiencies and create a fully utilized warehouse.
Interested in learning more about utilizing your warehouse efficiently? Check out our blog, "Optimizing Your Labor: 4 Things Warehouse Managers Must Do."