Warehouse Set-Up 101: Optimized Large Warehouse Layout
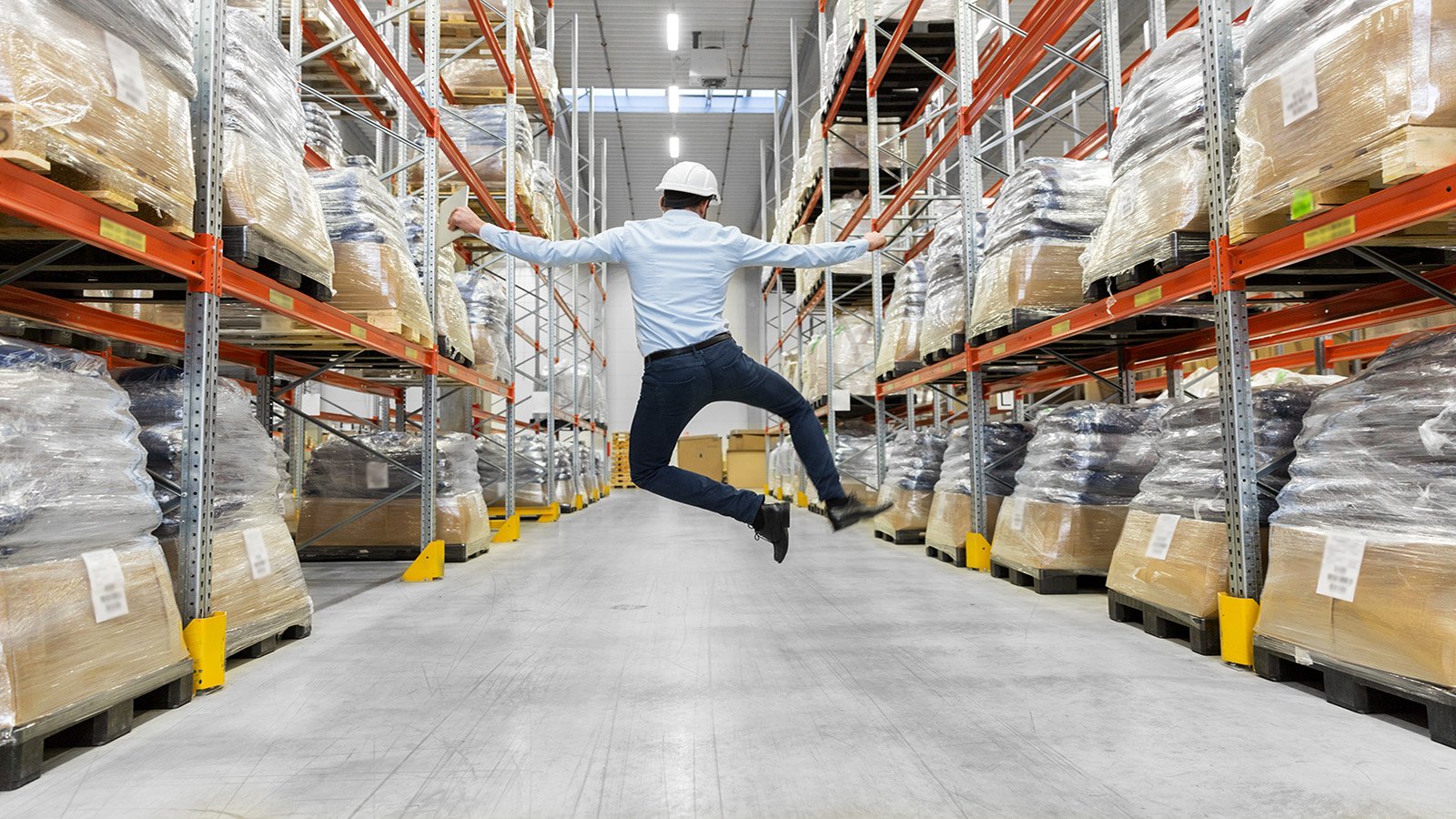
As a business ramps up its operations, it will naturally outgrow the space it’s in. With a larger warehouse (100,000+ sq. ft) comes more inventory, more people, and more machines moving around. To control the chaos, you’ll need a warehouse layout that is efficient and streamlined. It needs to flow, moving product smoothly and effortlessly until it leaves the building.
The bottom line on warehouse layout is literally about your bottom line: product out the door means money in your pocket. Anything that blocks the flow can cost you money.
The challenges in the layout for a large warehouse are basically the same as those for a small warehouse, just on a much grander scale. It’s the difference between a two-lane country road and a busy interstate highway. Traffic follows the same patterns, but the volume increases. For your warehouse, the greater volume of traffic means danger of bottlenecks, gridlock, and even the occasional collision!
Mapping out the flow in your large warehouse layout—from start to finish—is essential. Let’s take a look at the best roadmap to follow for laying out a large warehouse.
An Ideal Warehouse Layout for a Large Warehouse
The best warehouse layout is configured to create a clear, uninterrupted flow of goods from one area to the next and ultimately out the door. In a large warehouse layout, those areas are:
- Receiving
- Storage
- Picking
- Value-Added Area
- Packing
- Wholesale Staging
- Shipping
These areas are largely the same as those of small or medium-sized warehouses with a few key differences. Naturally, each area will be bigger. And there will likely be more packing and shipping stations, more storage shelves…more everything.
Second, the scope of your business might introduce new tasks that take up some of that formerly free space. For instance, you start selling products wholesale. Or you offer some value-added features like kitting, personalizing, or some other form of customization or special packaging. The optimal configuration of your large warehouse will need to take these new procedures into account.
Standard Procedures Are Essential
An important element in our highway analogy is the rules of the road. As your business grows, it becomes increasingly important to set standard operating procedures and communicate them to your staff.
These procedures may include who does what, where, when, and in what order. Having staff move via a certain path every time they do a task will help establish traffic laws for your workers.
The efficiency of your warehouse set-up hinges on everyone following their set path. The right layout should both limit the steps workers take and the times they handle a SKU. You want to eliminate roadblocks like:
-
Cross-traffic (people or machines crossing each other’s paths; increases the chances that someone has to stop—or worse, that they collide)
-
Doubling back (travelling the same space over and over is super inefficient.)
-
Traveling farther than necessary (eliminate loops, back-and-forth travel, etc.)
Receiving: The On-Ramp of Your Warehouse Highway
Because your sales volume has increased, so has your receiving. Arriving materials need to merge smoothly onto the path you’ve mapped out. Luckily, a large warehouse is more likely to have separate docks for inbound and outbound shipments. This keeps received goods separate from those ready to ship, but you’ll still need to pay attention to how the receiving area operates.
Delivered goods should be offloaded to an area near the dock, parked out of the way of other operations. They shouldn’t stay in the receiving area for long, though; move them to storage in a timely manner.
Organize the storage area so items are grouped near one another in a way that makes sense for your picking process. For example, say there are three different components in a popular type of order. If possible, you want to locate all three in the same row of shelving rather than have your picker visit three separate rows to fill the order. Again, the goal is to create the shortest, most convenient route for your staff. Setting “pick paths” for an employee to follow each time he or she picks products is important.
Streamlining Storage and Down-Forward Picking
The opportunity for streamlining in the picking process really comes into play with your down-forward picking area. This area should be located close to your packing stations.
If you’re tuned in to your predictive analytics (and by this time in your company’s life, you should be), you know the velocity of your items. Your layout should reflect that velocity. Here’s how. Give commonly-ordered items priority parking—closer to your picking and packing areas. Park the less-popular items further away. Then, every night (or whatever works for your operation), move your high-velocity SKUs from storage to a down-forward pick area.
The down-forward picking area is like a 15- or 30-minute parking spot. It’s conveniently located near the driver’s destination, and it’s short term. As cars drive away, new cars take their place. In the same way, products in this picking area are picked and packed within a short timeframe and are regularly replenished.
In contrast, the bulk storage area is more like long-term parking at an airport parking lot. The time a car will stay varies, but it won’t be leaving immediately. This is the place for items used less frequently or for bulk product that gradually gets moved to the down-forward picking area.
Adding Value Adds a Step
As business grows, you may have the opportunity to add another revenue stream by offering special “value-added” features. These features could include grouping items together to sell as a kit, monogramming or personalizing, gift wrapping, etc. Your warehouse layout will need a designated space to perform these activities.
The ideal location for a value-added area is on the path from the picking area to the packing area. That said, if most of the products get packed without the value-added service, the value-added area should be near that path but maybe off to the side. This way, the majority of items still flow easily from picking to packing. Those needing value-added attention simply take a short detour to the designated area—like getting off the highway at a rest stop—and then get back on the road to the packing area.
A Place for Packing
With packing, we’re (again) striving for an even flow. Products should enter the packing area at one end and exit at the other (the staging area for shipping). If your company has the volume to justify a large warehouse, you almost certainly have room for more than one packing station. This allows multiple orders to be packed at once. So when an order needs special packaging or is large and complex, it won’t cause a traffic jam. Other orders can “pass on the left” through the other packing stations on their way to the ship staging area.
Preparing Products for Bulk Wholesale
Another new part of the process for a growing company might be bulk wholesale sales. This addition requires a wholesale staging area in the warehouse layout. You’ll need to set aside ample room for packing pallets of goods for shipping. The area may also need to accommodate strapping or shrink-wrapping equipment or room for a forklift to maneuver.
This wholesale staging area should be easily accessible from storage, down-forward picking, or packing, depending on how you store these items. Wherever it fits in your space, remember to keep it on a path to shipping that’s logical and efficient.
Signed, Sealed, and Ready for Delivery
Finally, your orders make their last stop before leaving the building—the ship staging area. Things may hang out in this “parking lot” for a short time before being picked up. In the layout for a large warehouse, this area should be as near to the outgoing dock door as possible, without interfering with any other operations of the warehouse.
When trucks arrive to pick up your shipments, both individual orders and pallets should be easily accessible. Once again, efficiency and flow are important. The easier it is for products to be loaded onto trucks, the better.
Making Your Large Warehouse Layout Work
Moving from a cramped space to a large warehouse may feel like the answer to all your productivity problems. But it’s not quite that simple. It’s crucial to design a layout for a large warehouse that offers the most efficient use of space, or you’ll feel it in your bottom line. You need to create a logical flow of products through the space. And no plan is complete without clear paths and procedures for your staff to follow.
Not only should you plot your roadmap out on paper, but you should also test it by doing a dry run. Do your pre-set picking routes make sense? Are people and vehicles staying out of each other’s way? Does your machinery have the clearance to maneuver around corners? It’s best to find and fix any of these issues before you start using the space.
No matter the size or shape, most warehouses can fit the layout components we’ve described. If your warehouse has challenges that we haven’t addressed here, let us know. We’d be glad to help you find the right layout solution to optimize your space.