What Is Warehouse Slotting and How to Do it Better
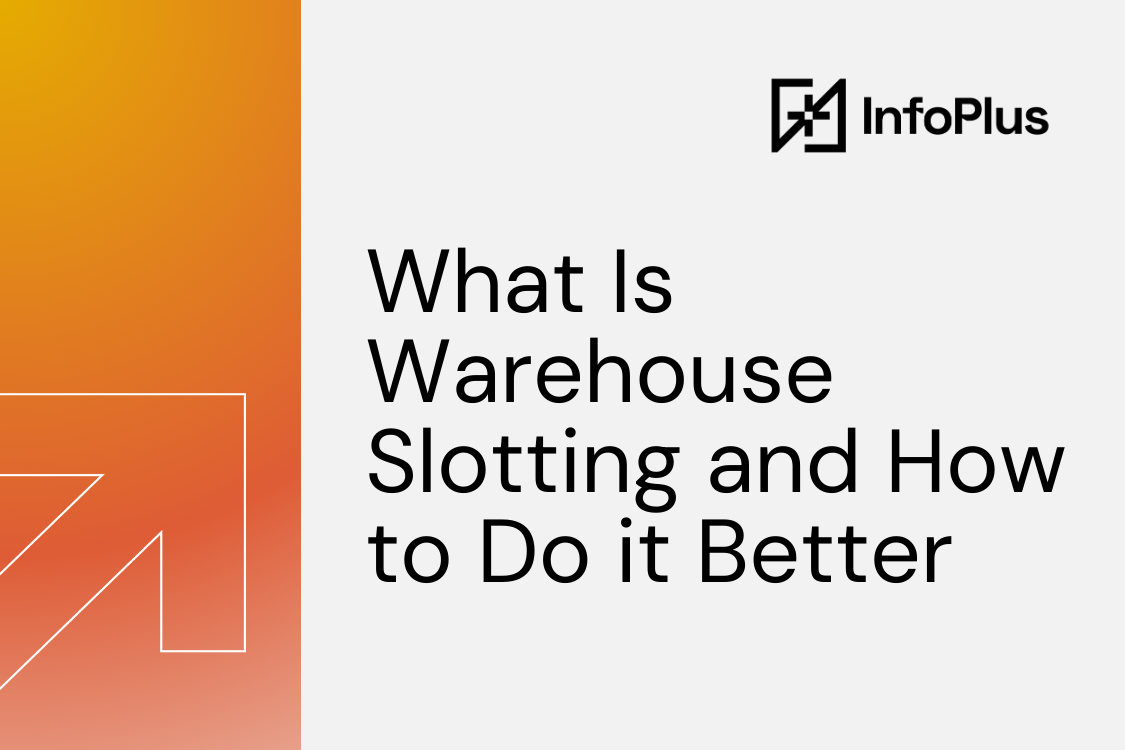
Inventory management and fulfillment tend to get a lot of attention in logistics circles, while receiving and put-away—in other words, slotting—are much less discussed. Together, all of these are necessary for the steady flow of products through the warehouse.
Warehouse slotting is the intentional, strategic organization of the inventory in a warehouse or distribution center. Items are arranged to optimize accessibility, picking speed, accuracy, and storage capacity. The overall goal is to make both fulfillment and replenishment as efficient as possible.
To understand the concept of warehouse slotting, look no further than an ordinary kitchen. While a cook could conceivably pile tools and ingredients randomly in cabinets and on countertops, a lot of time will be wasted searching for items. Getting a meal prepared and on the table is not going to be quick or easy. A better strategy is to assign things to a specific place, with the most-used items within easy reach.
This solution is obvious at home, but the same rules apply in a warehouse—albeit on a much larger scale. Warehouse slotting is an essential part of efficient operations, and the stakes are much higher than what to have for dinner.
What is Slotting in Warehouse Management?
Warehouse slotting goes beyond simply finding empty shelves or floor space for items as new inventory arrives. It needs to be part of an overall warehouse layout and management strategy that is geared toward finding and fixing inefficiencies.
While the basic concepts of warehouse slotting are easy to grasp, truly efficient slotting is complex and requires collecting data and crunching numbers. Decisions about what goes where consider each item’s velocity, dimensions, weight, grouping, and more. The practice gets more complicated with a larger area, more items, and additional product constraints and requirements.
When a company is small, managers can plot out a rudimentary slotting plan on a spreadsheet. However, once the business (and its number of SKUs) grows, slotting decisions need to be automated. Warehouse management software can help with the task.
What is Macro Slotting vs. Micro Slotting
Warehouse managers sometimes make a distinction between macro slotting and micro slotting.
Macro slotting refers to optimizing the overall layout of a warehouse. At Infoplus, we simply call this “warehouse layout” and have written about it extensively in our series on small warehouse layout, medium warehouse layout, and large warehouse layouts.
Micro slotting refers to how individual items or pallets are placed in specific locations in the warehouse (from the zone down to the specific shelf). This organization of SKUs and groups is what we mean when we talk about slotting.
Readers may encounter these two terms when reading up on slotting best practices, so it’s important to understand the difference.
Benefits of Efficient Warehouse Slotting
Just as an orderly kitchen can simplify meal prep, successful warehouse slotting can make order fulfillment easier, faster, and more accurate. This adds efficiency across the board.
The following results provide some clear justification for implementing slotting for the first time—and for reviewing and overhauling existing slotting strategies:
- Increases productivity. When pickers know exactly where to find what they’re looking for, they’ll fulfill orders faster. A well-organized warehouse also cuts down on bottlenecks and traffic jams. For example, proper slotting can set up a forward-picking area for high-demand items. Or it can keep heavy items in an area where forklifts don’t have to wait for on-foot workers to get out of the way.
- Decreases travel time. Every step a worker takes costs time and therefore money. If a worker has to pass a bunch of slow-moving items to get to those purchased more often, that’s a sign of inefficient slotting. Appropriate slotting shortens the distance workers must travel for both picking and replenishment.
- Improves visibility. Good slotting practices make it easier to see at a glance what items are stored in a zone and where. In a broader sense, it provides a better picture of how much is on hand. Along with inventory management software, this visibility can cut down on over-ordering or running out before replenishing.
- Reduces errors. When everything is slotted in its proper place it cuts down on human error during the picking process. Workers can spend less time hunting for items and examining them to verify they have the right thing.
- Makes the best use of space. Consider the shelves at the local supermarket. Items of various sizes and shapes fit together on shelves with little or no empty space. And when everything is orderly instead of cramped and cluttered, it seems more spacious. When slotting is done right, it’s surprising how much more usable space becomes available.
- Maximizes safety. Storing items in an efficient manner minimizes the chance of damaging products. For an extreme example, good slotting would never position heavy metal car parts on top of glassware. Slotting can also prevent injury to workers. Lifting bulky items off of a high shelf is much more dangerous than picking them up off the floor. And in general, cluttered, disorganized spaces are accidents waiting to happen.
Warehouse slotting provides an organized environment that optimizes productivity for put-away, picking, and replenishment. These lead to more efficient operations that have the potential to improve fulfillment volume and lower labor costs, both of which will show up in the bottom line.
Warehouse Slotting Best Practices
Warehouse slotting is obviously worthwhile, but how do you go about creating the right slotting strategy? The process involves gathering data on each SKU. The following data points will help in deciding how to slot items appropriately:
- The level at which the item will be picked (single piece, case, full pallet)
- The storage medium the item will be picked from (pallet rack, shelf, carton)
- Cube size and weight of the item
- The item’s velocity (predicted future velocity is preferable to past data)
- Seasonal fluctuations in item’s velocity
- Special storage requirements
- Product affinity (SKUs most often purchased with the item)
This data will inform how you go about your warehouse slotting strategy. Now, let’s cover each item in more detail. For more information on warehouse slotting best practices in your warehouse, take a look at this piece, "8 DC and Warehouse Slotting Considerations for More Efficient Warehouse Operations” published by Cerasis on their blog.
Item level and storage medium
SKUs picked by the full pallet will require a forklift, whereas single pieces won’t. It makes sense, then, to store pallets separately from cases or broken cases (individual units). This way, forklifts can move their pallets without interfering with single-item pickers and vice versa.
Item level and storage also dictate what kind of equipment will be needed for picking (forklift, pallet jack, cart, etc.). Pickers will know which kind of equipment they’ll need simply by the area in which the items are located.
It’s also worth noting that there is a “sweet spot” that is easiest for pickers to see and reach when picking individual items. This area is between the chest and knees of an average person. Slot high-velocity SKUs here on shelves for easiest access. Slower-moving SKUs should be out of the way, with the heaviest SKUs as close to the floor as possible.
Cube size and weight
How pallets, cases, and individual items fit in the warehouse is a function of the SKU’s cube size and weight. Broken cases will go on shelves. Exact measurements of each SKU are necessary for these slotting decisions.
Special consideration should be given to excessively large or heavy items. Moving these will be more difficult and time-consuming, so choosing a location close to the shipping dock is usually preferable. Cubic velocity is a helpful data point, as it takes both size and location into account, measuring the average quantity ordered over time, product dimensions, and item level.
Predicting Velocity
The general rule of thumb in slotting is, “fast-moving SKUs stay accessible and slow-movers stay out of the way.” A down-forward picking area accomplishes this by keeping popular items close to packing and shipping, cutting down on travel time for pickers.
Most warehouse managers can get some idea of their item velocity using “ABC slotting.” This looks at the number of each SKU ordered over a set period of time—usually 30 days.
The top 50% are designated as “A,” the next 25% as “B,” and the last 25% as “C.” (Seldom ordered items that didn’t make the list during the set time period are flagged with a “D”).
These designations determine the arrangement of items with the “A” items easiest to reach in the down-forward picking area. “D” items are stored farthest away, with “B” and “C” taking up the spaces in between.Special Storage Requirements and Product Affinity
Instead of looking only back at the past chosen time period, warehouse management software uses predictive analytics to project future needs. Barbecue grills and patio furniture sell like hotcakes in the spring and early summer. Boots and snow shovels sell a lot faster in fall and winter. By studying market trends and seasonal spikes, managers can get a much clearer view of the SKU velocity to come and slot items accordingly. (Our Allen Brothers case study is a good example of predicting and accounting for seasonal variations.)
Special Storage Requirements and Product Affinity
Finally, items need to be grouped together into zones based on their specific storage requirements. Some examples:
- High-security, high-value or heavily regulated items (electronics, jewelry, alcohol, THC products) must be in a secure (caged) zone.
- Temperature-sensitive items require temperature-monitored environments.
- Perishable products need to follow FIFO rules for picking and replenishing as well as strict disposal rules when they expire.
- Potentially toxic materials must follow safety protocols and be stored separately.
These special storage requirements will determine where items are slotted. When there are no specific requirements, zones can group together items that are frequently ordered together, also known as “product affinity”. For example, slot shampoo, conditioner, and other hair products in the same zone. Or store razors, shaving cream, and beard-trimming tools together. Since shoppers might order a few different products in these categories at the same time, grouping them together creates a shorter pick path for workers.
Warehouse Slotting Algorithms
Warehouse slotting is an essential component of warehouse operations. It keeps the space organized and efficient, allowing employees to do their jobs more effectively, with less wasted time and effort. While the concept and its benefits are easy to understand, putting it into practice is difficult without the right tools.
Infoplus warehouse management software takes on the task of gathering, organizing, and analyzing the data from SKUs, order history, and picking levels, then creating a slotting plan that makes sense. Infoplus can also take those insights a step further by providing recommendations for pickpaths, rack labeling, and other aspects of inventory management.
When it's time to assess or revamp your company's approach to warehouse slotting, get in touch with our team.