Leverage Machine Learning to seamlessly transforms your warehouse data into actionable intelligence, providing unparalleled visibility and control over your fulfillment operations.
What is Insights?
Infoplus Insights is a powerful analytics tool that leverages the prowess of machine learning and user defined SLA's (service level agreements) to provide our users with invaluable insights, patterns, and connections within order data. Unlike conventional analytics tools, Infoplus Insights is not confined to historical analysis; it actively mines order data to unveil real-time trends and patterns and ensures the right orders are being focused on, and done so in the most cost effective and efficient way.
Just like rate shopping where you shop around for the best shipping rates or fastest delivery times, Infoplus Insights works similarly but for your entire fulfillment process. It ensures that your operations stay flexible and adapt to the changing patterns of orders and volumes.
With order volumes and compositions shifting day by day or even hour by hour, being able to quickly identify trends and make informed decisions becomes crucial. Insights goes beyond this by not only identifying trends but also showing you the most effective ways to pick orders. Many warehouses fall into the trap of sticking to a single method, assuming it's the most efficient. However, this one-size-fits-all approach is often not the most cost-effective or efficient. Insights empowers you to break free from the norm, providing real-time data to guide you towards the best picking methods based on the current circumstances. It's about staying agile, optimizing your strategies, and getting the most value out of your fulfillment operations.
How Does Insights Work?
Machine learning is the driving force behind the remarkable capabilities of Infoplus Insights, making it a cutting-edge solution for warehouse management. At its core, machine learning is a subset of artificial intelligence that enables systems to automatically learn and improve from experience without being explicitly programmed. In the context of Infoplus Insights, machine learning algorithms analyze vast amounts of real-time order data, identifying patterns, correlations, and trends that might be challenging to discern through traditional methods.
This dynamic learning process empowers out users to adapt and evolve, ensuring that the insights provided are not static but continually optimized based on the ever-changing landscape of orders and volumes. By harnessing the power of machine learning, Infoplus Insights can predict fulfillment outcomes, recommend the most effective production models, and adapt strategies in real-time to meet shifting customer demands and external variables. It's the intelligent backbone that transforms raw data into actionable intelligence, guiding businesses toward enhanced efficiency, cost-effectiveness, and operational excellence in their fulfillment operations.
To make the most of this powerful tool, users can configure essential settings to tailor it to their unique business environment.
How to Access Insights
The primary screen for Insights is called "Open Order Insights". This screen can be found by clicking the Insights icon on the left navigation bar of the dashboard. You can also search for it in the quick actions menu. If the feature is currently locked, have your Infoplus administrator reach out to support for further assistance, we're happy to get it turned on for you.
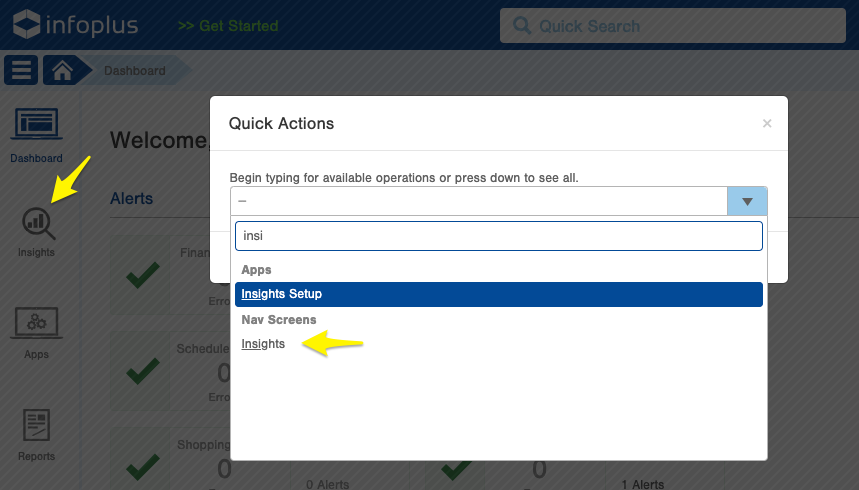
NOTE: The primary "Open Order Insights" screen is only available to users with type "3PL Admin". Customer users will not be able to access this screen.
In addition to the Open Order Insights screen, there are some additional fields to the Orders table: SLA Date, SLA Status, Production Type, and Similar/Identical Orders. These fields are visible on the Viewing Order screen, in the box shown below. SLA Date, SLA Status, and Production Type can also be used on the Orders query screen:
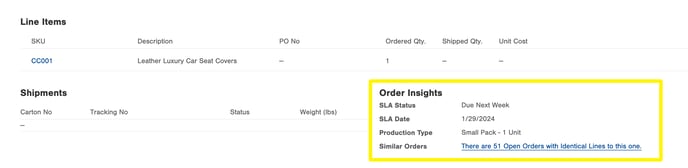
What Data is Needed?
Warehouse Service Types
-
Insights clients can define their own Warehouse Service Types. Ideas are like "B2C", "Retailer", "Same Day Rush", "LTL".
-
The table for doing this is simple - just a Name and optional Description.
-
You can also set, on a LOB and an Order Source, what default Warehouse Service Type should apply to new orders (i.e., "This is my Retailer order source" or "This LOB is always LTL orders").
SLA Days & Times
-
The Line of Business table has fields for defining the default Service Days and Cutoff Time for the LOB. Note, 0-days means "same day if entered before cutoff time".
-
This table also has a sub-table where override rules can be setup for an LOB. This allows users to specify by Warehouse Service Type, Warehouse Service Level, Backorder Status, and additional SLA service days & cutoff times.
-
i.e., "rushes must be entered by noon" or "LTL orders have 5 days of service time".
-
Warehouse Timezone
-
The warehouse table has a new timezone field, to drive if an order is before or after the cutoff time when its SLA date is being computed.
Business Days
-
SLA Date calculations only consider days when the client is working. 2 tables under the Insights Setup app allow us to set these up:
-
Standard Business Days - defines a client's standard week (true = work that day, false = off that day) - will be pre-populated as M-F.
-
Non-Business Days - define essentially holidays or other exceptional closed-for-business days. Must be set up every year.
-
Typical Non Business Days:
-
1/1/20
|
New Year's Day
|
12/25/19
|
Christmas Day
|
12/24/19
|
Christmas Eve
|
11/29/19
|
Day after Thanksgiving
|
11/28/19
|
Thanksgiving
|
9/2/19
|
Labor Day
|
7/4/19
|
Fourth of July
|
5/27/19
|
Memorial Day
|
4/19/19
|
Good Friday
|
Production Models
- Production models are used when estimating the steps and touches for every order. With that being said, it requires our clients to provide a detailed list of all of their processes as well as assign a “cost” to each step. An easy way to use the cost feature is to think of the step in terms of seconds. For example, if step 1 is “Hit Execute” in the Insights screen, that might take 20 seconds, so the cost would be 20. Step 2 is to print the documentation and deliver it to the picking team. This step might take 2 minutes, so we assign the cost as 120. Once we have a cost associated with every step of the process, we have a true view of how much labor is involved.
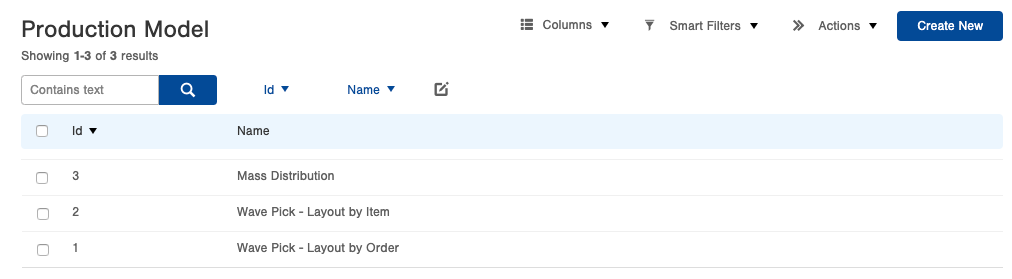
If you plan on setting up a Mass Distribution production model, make sure to specify the corresponding validation function. Currently, Mass Distribution is the only validation available. This function makes sure that all orders being analyzed are identical before recommending a mass distribution production type for an order group. (We’ll explain this in greater detail later on).
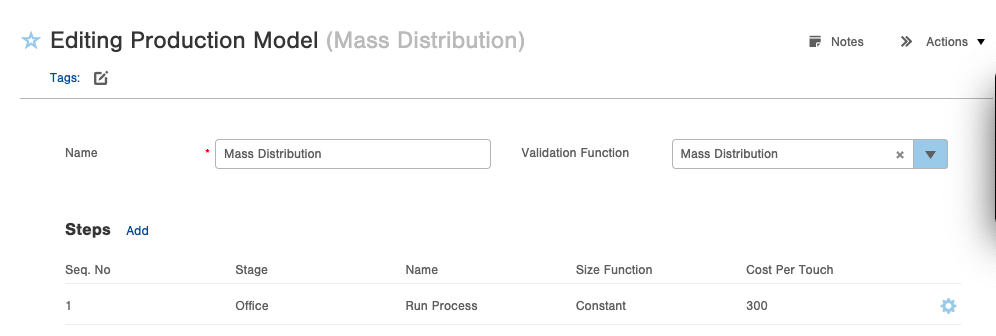
Example Production Model:
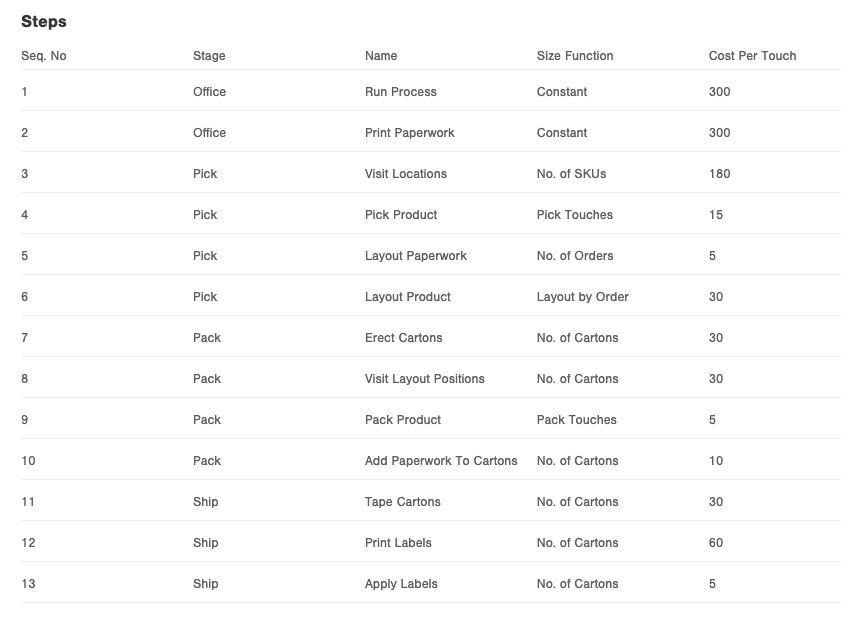
