3 Cost Efficient Ways to Optimize Your Warehouse
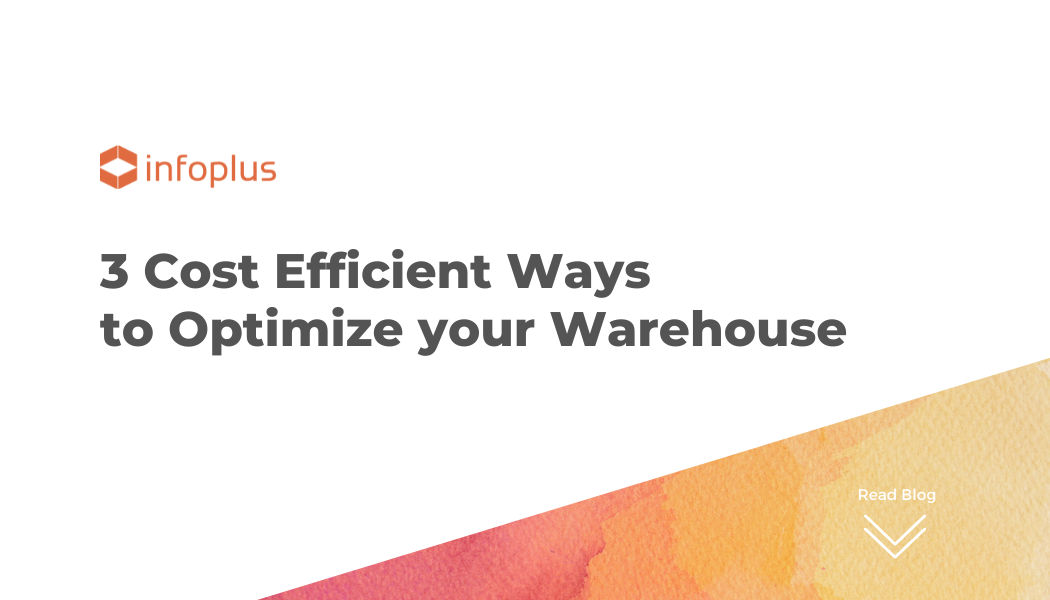
Running a warehouse is a complex challenge. Operations managers juggle efficiency, order accuracy, budgeting constraints, and more on top of their routine tasks.
Excess materials, too many workers driving up labor costs, and bulky technology may be burning a hole in your pocket. You can save money in your warehouse operations by optimizing the layout and standard material and labor costs.
Have you made the most cost efficient decisions for your warehouse operations? Three of the most efficient ways to reduce your spending include:
- Using less material
- Cutting labor costs
- Upgrading your tech stack
Warehouse layout optimization is no small task, but by optimizing a few key components in your warehouse, you can save money and potentially increase your ROI.
Use Less Material
When your SKUs are picked for packaging, material may be wasted when there's no standard for how much to use.
If your warehouse management system (WMS) has the dimensions and weights of all the items that will get boxes, cartonization can pre-determine the packaging size needed for each item, lowering your waste.
Once cartonization sets best practices in place, don't overstuff your items to use even less material and experience distinct changes in how much you pay for material.
Increase Labor Efficiency
More workers may not mean more inventory out the door. To understand the productivity of your workers, it's vital to consider these three statements and measure them against your current warehouse operations workflow.
- Items are located in easy access to the allocation of orders,
- Picking, packing, and shipping are assigned to maximize labor
- Employees are well trained on picking, packing, and shipping methods.
With these questions in mind, you could cut labor costs by planning an efficient warehouse layout. From there, schedule enough staff to meet your weekly needs. Soon, you’ll likely see a natural decrease in labor costs.
Optimize Your Pick Paths
A pick path is the method and route a picker takes to efficiently pick SKUs off their shelf and deliver them to sorting or packaging, depending on the pick method you choose to implement. By optimizing the pick path to follow the fastest route from receiving to sorting, you’ll save your workers time, making them more efficient.
There are three picking methods and plenty of variations you can choose from. Each warehouse needs to choose the picking method or methods that fit their needs, access, and tools available. A WMS can actually tell you the best way to pick based on these factors.
One way to achieve this is forward picking. Forward picking is taking the inventory you sell the most of and grouping it in the front of your warehouse or closest to your packaging and sorting area.
This way, pickers won't need to pick the entire warehouse on a regular basis, saving on steps and increasing efficiency.
Store Inventory Closer Together
Think about your racking system. If your warehouse uses both machine and foot traffic, organize your racks based on the frequency of fulfillment for your items. Items that are less frequently orders on higher racks, while items that are most frequently ordered are on lower racks, so you can balance foot traffic vs machine traffic to pick orders.
On a similar note, create a seamless flow in your picking method by storing inventory together that’s commonly purchased as a unit. This will take a trip off your picker’s path and cause order fulfillment time to decrease.
Schedule Workers Efficiently
With picking methods in place and inventory stored closer together, calculate how many workers your warehouse needs for order fulfillment every week. With unnecessary steps eliminated, the number of workers to get the job done should decrease.
Efficient warehouse planning at a fraction of the cost makes all the difference in the efficiency, accuracy, and accountability of your warehouse fulfillment. However, manually creating a base material standard, optimizing pick paths, and researching inventory data costs you something as well: your time.
Upgrade your Tech Stack
Automation makes even small tasks faster. With a powerful warehouse management system (WMS), implementing cost-saving best practices doesn't take time from executing important warehouse operations from you or your employees.
Save time now and money down the road using your WMS to:
- Gather SKU data to determine forward and storage locations
- Utilize cartonization to save time in your packing operations
- Analyze and implement efficient picking methodologies
A WMS works with you to optimize your warehouse layout for the most efficient processes. It also eliminates the need for bulky technology, like printers and scanners, with everything stored on the cloud.
When you’re planning your warehouse or looking for an upgrade in your processes, remember saving money is easier than you think. With the right processes and technology in place, your ROI will benefit from using your warehouse layout efficiently.
Interested in learning more about how to optimize your warehouse layout? Check out our blog on Lean Warehouse Management Practices.