Efficient Warehouse Storage: Inventory Storage Tips
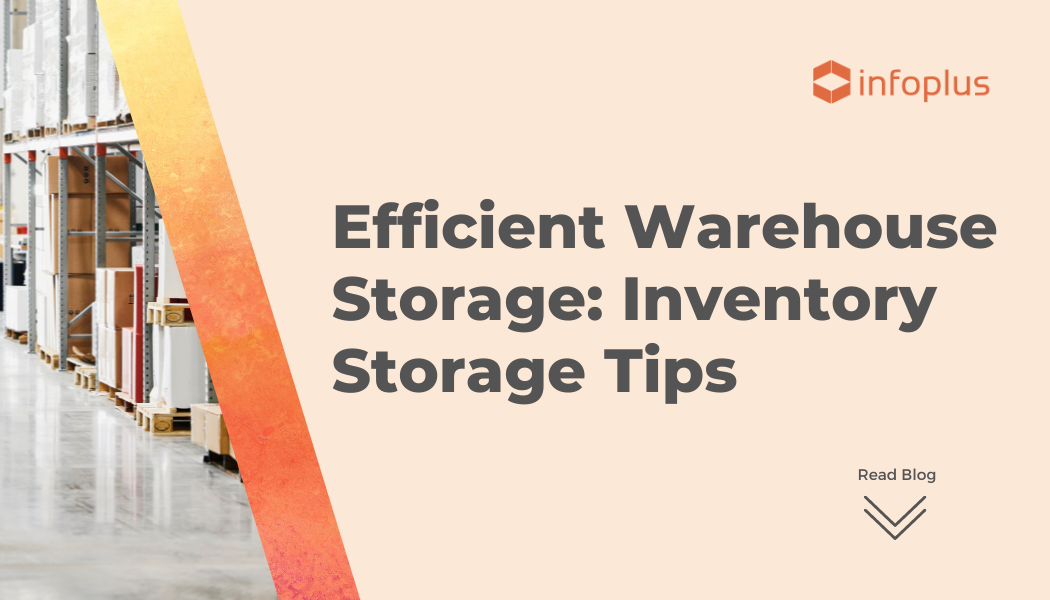
Managing inventory is a game of trade-offs, and nowhere is that more obvious than when planning the layout of the storage area.
To take an extreme example, you could pack all of your inventory together, leaving no space between items or SKUs. That would be an efficient use of the space, for sure—but it would be a nightmare for your pickers, not to mention a good way to lose important lot information. The best use of your space balances the needs of your picking and putaway with the amount of “dead” space in the warehouse.
Inventory storage, then, is not simply a matter of finding shelf space for all of your SKUs. It is a game of balance where you will have to consider item velocity, replenishment rates, mixing rules, and storage equipment capabilities.
6 Simple Tips for Efficient Warehouse Storage
Here, then, are some best practices for assigning storage based on these considerations.
- Popular or fast-moving items should be stored in such a way that they can be easily accessed by pickers, even when the warehouse is busy. Forward staging should be used when it makes sense (see below).
- Like items should be stored together when possible, with individual lots, shelves, and racks clearly labeled.
- Follow best practices for warehouse slotting when doing putaway for items; this can take time, but is well worth it in terms of space saved.
- Mixing rules should be adjusted for the types of items involved. For example, a batch of low-cost, homogenous items like ping-pong balls can be mixed in any way that is efficient, while pharmaceuticals would need to be separated by production lot and date of receipt.
- Shelf and pallet arrangements should make it easy to pick the correct items, depending on whether you use FIFO, FILO, or some other inventory accounting method.
- Storage areas and racks should be aligned to anticipate new incoming products.
All of these best practices should be implemented in a way that minimizes the number of times items have to be “touched”—including being inspected or moved. This cuts down on the possibility of human error.
Advanced Tip: Forward Staging
Forward staging is the practice of having a set amount of stock in a forward location in the warehouse, close to where packing and shipping will occur. When an order for one of these items comes in, an employee will choose items from the forward location first. The idea is to minimize trips to more remote locations in the warehouse, as well as the distance a picker has to travel to get an item.
Forward staging makes sense for popular items—items with “high velocity.” The forward location might have, for example, enough items to fulfill orders for a particular day, getting replenished from a larger stock elsewhere in the warehouse at the end of the day.
Ideally, your warehouse management software (WMS) would be set up to track stock in the forward location, issuing a Low Stock warning when items get low and alerting the appropriate parties that a replenishment is needed. This “replenishment threshold” can be set depending on how fast orders are moving and how long it takes to get the replenishment.
Forward staging does not have to occur in the same facility as storage. It is a common practice to have a larger off-site facility that is out of the way (usually meaning cheaper square footage) and then have a forward staging area closer to shipping outlets (meaning faster shipment and happier customers). This strategy can save a seller both time and money if the two locations can be successfully coordinated.
Items that do not move as quickly probably do not need to be staged. Also, items that are difficult to handle—for example, ones that are heavy or cumbersome—probably should be stored in a standard pick location that gives easy access. Items that get ordered infrequently, or that take some effort to pick, should not “get in the way” of faster-moving orders.
So, when deciding what items to place in a forward staging area, ask:
- Which items are ordered most frequently/have the highest order velocity?
- Which items are stored in the most remote areas of the warehouse (or at a separate facility)?
- Is the item in question particularly heavy or cumbersome? Does it require any sort of special handling?
- Are there any items where a surge in orders is anticipated—for example, due to seasonal variation or weather events?
Advanced Tip: Taking Locations Offline or Adding New Ones
No matter how much time you spend trying to set up the perfect storage system, changes will be inevitable. The key, then, is to have a flexible system that can keep things running smoothly even when changes need to be made.
This is where the right warehouse management software makes a big difference. Making changes to locations is simply a matter of routing workflows correctly in recognition of that change. The better your software can update and route your workflow, the better it will accommodate a change.
For example, suppose you have added a new section of shelving in your warehouse. You should be able to move inventory to that section easily, if needed, and route incoming inventory there as well. In Infoplus, this can be done through a simple command. You can also reserve storage areas for damaged goods and returns, or scale down space when not needed.
Advanced Tip(s): Getting the Right Storage Equipment
Storage equipment encompasses everything from large warehouse shelves and racks to small bins and drawers. Getting the most out of your warehouse storage means making maximal use of your warehouse storage equipment—and having the right equipment to begin with.
For example, when deciding on warehouse storage equipment:
- Think in 3D. If you have room, taller warehouse racks and shelving can provide additional, valuable storage space.
- Make note of weight limitations. Make sure warehouse racks and warehouse shelves can accommodate each product’s weight.
- Choose the right containers for smaller items. These can be bins, totes, bags, or tubs. Consider if these containers need to be stackable, how heavy each might get, and how often they will need to be moved.
Automating Storage and Workflows with Infoplus
Storage challenges are fairly easy to handle when your warehouse or storage facility is small. But as your storage needs increase, so does your need to automate many of the processes that touch your inventory.
Infoplus Commerce is warehouse management software (WMS) that can make your storage much more efficient—along with the rest of your warehouse. It scales easily with your organization, so you can invest now and have software that will grow as you grow.
Contact us today for a demo.