How Much Does a Warehouse Management System Cost?
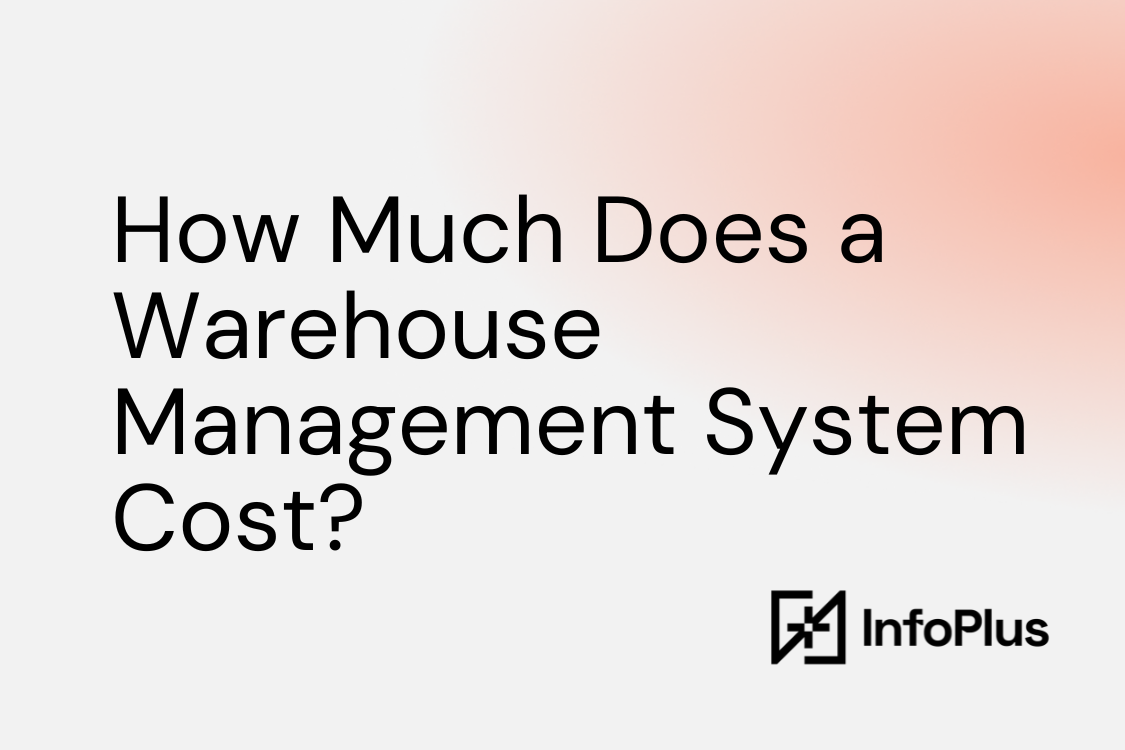
Warehouse Management Software (WMS) can do a lot to streamline ordering and manage inventory, but its high cost often keeps smaller businesses away. Sure, WMS provides the tools and capabilities to optimize inventory management, order fulfillment, and overall warehouse layout and processes. But many businesses delay implementing WMS precisely because they are grappling with the question of cost.
This isn’t just because WMS is expensive. Different prices from different vendors can vary wildly. So, to make an informed decision, a business of any size has to think hard about the value that they are wanting—the benefits they get vs. the price tag. And sometimes, more expensive software is a better value than lower-priced software if the value is there.
Types of Warehouse Management Software: On-premises vs. Cloud-based
The type of WMS is the first factor determining the WMS cost. There are two types of WMS: On-premise and cloud-based. On-premise WMS is installed on servers within a business’s facility, while cloud-based WMS is hosted on external servers and accessed via the internet.
On-premise WMS typically requires a more significant upfront investment, as businesses need to purchase servers and other hardware plus licenses for each user.
Cloud-based WMS, on the other hand, is usually subscription-based and requires less upfront investment. You’re buying a package that includes a certain number of users and you don’t need servers and hardware other than internet-connected computers.
Comparing Ballpark WMS Costs
The vast range of software products, and the fact that every business’s needs are different, make it impossible to name a single price for warehouse management software. We can, however, provide a range of the average fees that a company can expect.
The following data is from Explore WMS, an independent resource for supply chain professionals. As you will see, there is a considerable difference between more economical software and top-of-the-line systems. These differences are due to several factors including the business size, features and functionality, and industry. We examine each of these areas later in the article.
Software Licenses: Purchasing a license outright starts at about $2,500 per facility for basic software. A comprehensive, enterprise-grade system with advanced features like full automation can cost between $20,000 and $200,000.
On-premises installation of licensed software typically costs an additional $2,000 to $10,000. Expect to pay 10% to 20% of the license fee for upgrades and ongoing support.
Subscription Software: Monthly subscriptions for SaaS products range from $100 to $500 per user, depending on the software’s capabilities. Obviously, the number of users will determine the overall cost.
Initial setup and customization may cost anywhere from $1,000 to $7,000. Support, however, is often included in the monthly fee.
Size of the Business
This size of the business is obviously a factor in the cost of WMS. The more users and facilities, the higher the price.
Another reason, though, is that the bigger the operation, the more likely it will need additional features that will increase costs. Keeping track of hundreds of SKUs for example, will require robust inventory management that handles mixing rules and allotment protocols.
Warehouse management software for a small business might be less advanced and therefore cheaper. They may not need every automation available, so paying for a lot of bells and whistles can be overkill.
No matter what the size of a company, if more advanced software can improve operations or save money, it will be worth the investment.
Features and Functionality
The features and functionality of WMS software can also impact its cost. Basic WMS software may only include inventory tracking and order management features. In contrast, advanced WMS software does so much more. Comprehensive systems can include automated packing, shipping, and data collection, predictive analytics, real-time visibility, and optimized warehouse layouts and pick paths.
WMS software with advanced features can cost more than basic WMS software since it requires more development time and resources. However, if a company needs these features to run its business effectively, they are worth the additional cost.
Industry
The industry a business is in can also influence the cost of its WMS. Industry often influences the features needed and therefore the perceived value of the software.
For example, suppose a company uses its WMS to manage the flow of raw materials through its facilities, ending with some light assembly before shipping. In this case, the company has more complex needs than another company that is simply storing and shipping finished manufactured goods.
Heavily regulated industries like alcohol and cannabis require a more advanced system. Infoplus WMS, for example, handles compliance, security, and special handling rules for these specialized products. The extra cost of these features is vital to running a business in these sectors.
Scalable Warehouse Management Software
As a business grows and evolves, so do its warehouse management and software needs. The right WMS should scale alongside the business, providing the flexibility and adaptability required to accommodate changes in demand, inventory, and operational complexities.
As your warehouse expands or your product lines diversify, a scalable WMS system can seamlessly incorporate these changes, ensuring your warehouse operations remain efficient and streamlined. A business that chooses software based solely on cost runs the risk of outgrowing its capabilities. Switching to a new system is expensive in its own right, with the cost of the new software plus the time for training and setup. Scalability minimizes the risk of disruptions and enables your business to capitalize on new opportunities and sustain long-term growth.
Customization
Some small businesses do fine with standard WMS features and settings. Others require more customization. Developing and setting up custom workflows can come at a higher cost.
But for a business that has special processes, it pays to find a WMS that allows for modifications, rather than trying to fit the proverbial square peg in a round hole. Settling for a cookie-cutter solution can hamper growth. Infoplus clients appreciate that they can customize not only the software’s dashboard but specific warehouse functions too.
Implementation and Training
Any new software will require implementation and employee training, which might be reflected in the overall cost. Like ongoing support, making sure to get off on the right foot has definite value.
When shopping for a WMS system, it’s important to consider the onboarding process. While software companies might not explicitly charge for training and implementation, there is an opportunity cost until things are completely up and running. Not only should training be thorough, it also must be efficient and responsive to offering additional help when necessary. Look for a provider like Infoplus, with onboarding procedures that set clients up for long-term success.
Next Steps
Weighing the cost of WMS software against the benefits is an important thing to remember. For example, a free or inexpensive WMS may work best if you’re just starting and need basic inventory management features. But suppose your business is growing quickly and needs advanced functionality like mobile access and data sharing capabilities.
In that case, you may want to consider an experienced WMS provider like Infoplus. Infoplus WMS delivers innovative, customizable functionality that makes warehouse managers happy, and at an unbeatable price that will satisfy the CFO. Contact our sales department to get your free quote.