Warehouse Set-Up 101: How to Setup Small Warehouse Layout
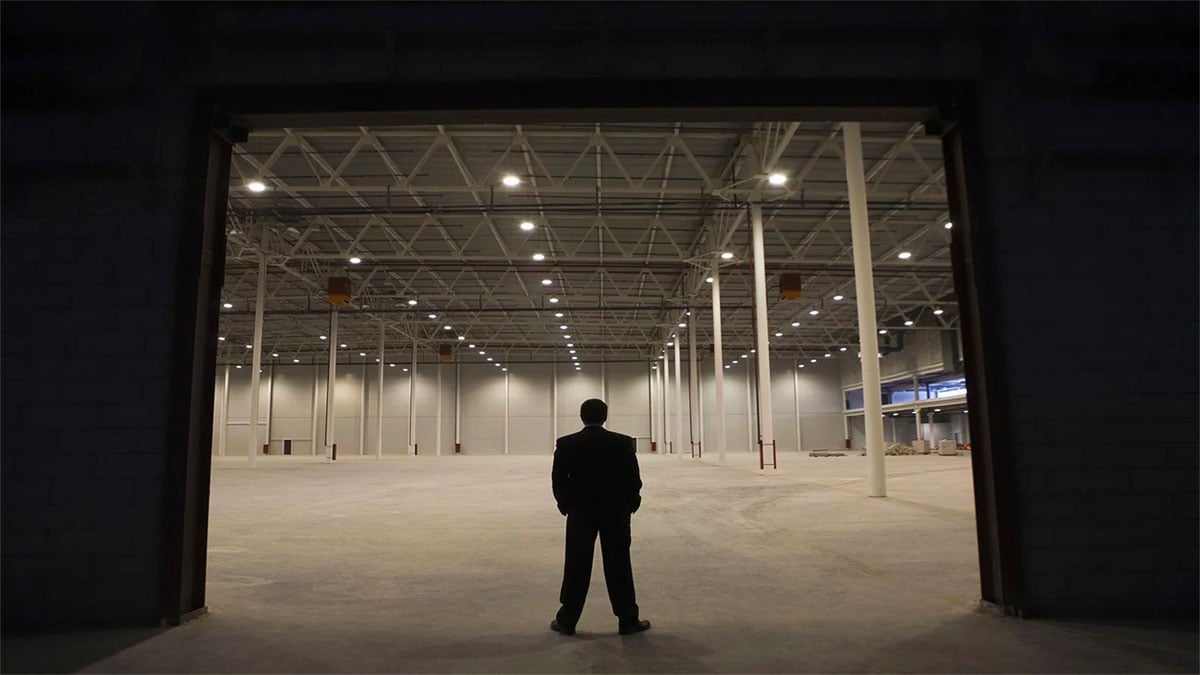
If you’ve recently bought or leased a smaller warehouse, I’ll bet you have hundreds of questions running through your mind right now. How to setup a small warehouse? How to design a small warehouse layout? How to organize a warehouse? How to optimize warehouse layout? Where should racks and pallets go? Where should the packing station be? And the shipping station? How to manage warehouse efficiently?
Designing a warehouse layout isn’t terribly tricky, but the devil is in the details. Every step a worker takes will cost you both time and money. The same goes for every time someone touches an item or changes their route through the warehouse.
Fortunately, there are some simple ways to optimize your warehouse layout to maximize its flow and efficiency. We’ll walk you through the main areas and the considerations that go into their placement and setup, particularly for a smaller warehouse owned (or rented) by a growing company.
An Ideal Warehouse Setup for a Smaller Warehouse
For the sake of our tour, we’ll assume you have a 10,000 sq. ft. warehouse that’s roughly square-shaped. Just keep in mind that your warehouse might not be exactly like that; it could be bigger or smaller, or the floor space might be some shape other than square. (We’ve run into our share of L-shaped warehouses!) More important than the exact specifications are the reasons behind our small warehouse layout design infographic.
A good warehouse layout will have a clear, uninterrupted flow of goods through five main areas:
-
Receiving
-
Storage
-
Picking
-
Packing and Shipping
-
“Free” Area
Remember, shipping should be your number one priority. Shipping product out the door is what grows the bottom line. And if that’s not happening efficiently, you can basically forget about everything else.
The Receiving Area: Don’t Bottleneck at the Dock:
In a smaller warehouse, chances are high that you have just a single dock for both shipping and receiving. Keep your eye on that, because bad things will happen when incoming stock gets in the way of outbound shipping.
Classic diners often have this same problem, as the wait staff brings food out of the kitchen using the same door that they used to go into the kitchen. You can imagine the mess that results when someone swings open the door as another person brings food out—it’s the stuff of comic legend.
Today’s retail climate makes this problem even worse, what with Amazon’s promise for 2-day delivery. It’s practically an industry standard now. Customers expect it. This means you just can’t afford to have products piling up in your shipping area. And so, everything else needs to be arranged in such a way that it helps—or at least doesn’t hinder—your shipping operations.
So, here’s your goal: avoid congestion at the dock. To make that happen, you need to offload incoming goods immediately into a receiving area right next to the dock area. Keep this receiving area separate from fulfillment and shipping. With this setup, an outbound delivery truck can pull up as soon as an inbound one pulls away. And you won’t have to worry about new inventory getting in the way of loading, either. Win-win.
Items should not sit in the receiving area for long, however. That’s what storage is for.
Storage and Forward Picking: Item Velocity Matters
Obviously, storage is the main reason you have a warehouse in the first place. But you can be smart about arranging your storage area so that your pickers never have to travel far for what they need. (Remember: Every step costs money!)
Reduce your warehouse travel time with a forward pick location. SKUs that are ordered more often—what we call “high-velocity” goods or orders—should have a given amount set aside in their own smaller storage area for easy access. That’s what the forward pick location is. This area should be placed as close to your packing stations as possible to minimize travel time and maintain the flow of goods through the warehouse. (Yes, I said that again.)
On the other hand, slower-velocity goods can be kept in a larger bulk storage area. Every night (or whenever makes sense—you know your best schedule), there should be movement from the bulk storage area to the forward picking area in anticipation of the goods that will be needed for the next day.
So as a general rule of thumb, the high-velocity area should have about a day’s worth of orders for every SKU (though slower-moving SKUs might stay in the bulk storage areas). This way, all the items that need to be picked on a given day will be readily accessible in the closer forward picking area.
Think of it like a public library: there are general stacks where most books are found, but most libraries also have easily accessible shelves for book club picks and new arrivals, both of which are checked out more frequently. The layout of your warehouse should do the same, shelving hotter items where they can be picked most conveniently.
(BTW, this is a great argument for why you need good predictive analytics to foresee what your item velocity is going to be like day-to-day. The better that information, the more efficient you can be in stocking your short-term staging area.)
At this point in the tour, we should note something important about the overall layout: how it optimizes pick paths.
Pick Paths: Aim for Single Lines of Flow
In a smaller warehouse space, it’s way too easy for everyone to run into each other or work on top of each other. The chances that people (and machines) get in each other’s way are highest during the day when warehouse workers are picking orders for packing and shipping. The ideal warehouse layout minimizes cross-traffic—preventing delays or reroutes—and optimizes overall flow.
To do this, create a linear path from the receiving dock, to storage, to the down-forward picking areas, to packing, and finally to shipping. There should never be an instance where this path doubles back on itself. Accomplish that and you’ll never have to worry that a picker bringing SKUs to the packing station crosses paths with stockers bringing inventory from the receiving area to bulk storage (a recipe for congestive disaster). Likewise, there should be minimal distance between the picking area and packing, lowering the chances of running into someone or having to deviate from one’s path.
If you find that you can’t create a single line of flow, it’s probably because you’re trying to fit everything into a straight line or a complete circle. You don’t have to be that precise. For example, a Z-shaped path that snakes from receiving to bulk storage, down to down-forward picking, and then out again to packing and shipping is perfectly fine. Just be sure to keep overall distances to a minimum when possible.
Leave Room for Packing and Shipping
We round out the tour of an optimal warehouse layout by looking at stations for packing and shipping. Yes, you need specialized areas for those and a separate ship staging area to boot. (We’ve seen too many warehouses where packing and shipping stations are a mere afterthought. That makes no sense, seeing as getting products out the door is the main activity for a warehouse operation!)
Packing should be arranged so that items come in at one end and finished packages come out the other. There should be a seamless flow from pick to pack to ship and then out the door. You should also have separate areas for “shipping” and “ship staging.” Once a shipment has the correct labels and shipping information, it should be set aside for two reasons: 1) to have it ready for pickup at any time and 2) to unclog the ship station and keep goods flowing. This set-up also keeps outbound goods out of the way when receiving.
Free Area: Plan on Room to Grow
Smaller warehouses are usually used by smaller companies—but that just means that there’s still a lot of growing to do. So when you’re planning a warehouse layout, you can’t leave out the opportunity to accommodate growth and change.
In other words, you need to plan on having some “free area” reserved, preferably somewhere in the middle of your layout.
When warehouse operations are tamer, this is simply empty space where people or machines can move freely. It offers both a buffer zone (between receiving and shipping and between long-term storage and staging) and additional space to move when things get busy.
As operations grow, this free space can be converted to other workstations in order to remove bottlenecks. For example, you could add a second line of packing and shipping stations to speed up those processes. Or you could conceivably use it for extra forward-picking of high-velocity items.
It’s the same strategy that a new couple has when they buy a three- or four-bedroom house: they’re anticipating a growing family. In the meantime, those extra bedrooms can help keep things open and uncluttered.
What if a Small Warehouse Layout Doesn’t Describe Our Operations?
OK, so your warehouse might not have the same challenges we are assuming here. Maybe your warehouse is small, but it has multiple docks or it doesn’t need to factor in space for growth. If so, check out "Warehouse Set-Up 101: Optimized Medium Warehouse Layout" for medium sized warehouse layouts and for larger-sized warehouses check "Warehouse Set-Up 101: Optimized Large Warehouse Layout" . One of these layouts might better suit your situation.
And if you have a unique situation—a particularly odd-shaped space, SKUs that need special storage, super-high-velocity goods, or whatever—feel free to reach out to us and we can find a custom layout that works for you.