How to Set Up an Efficient Receiving Area Layout!
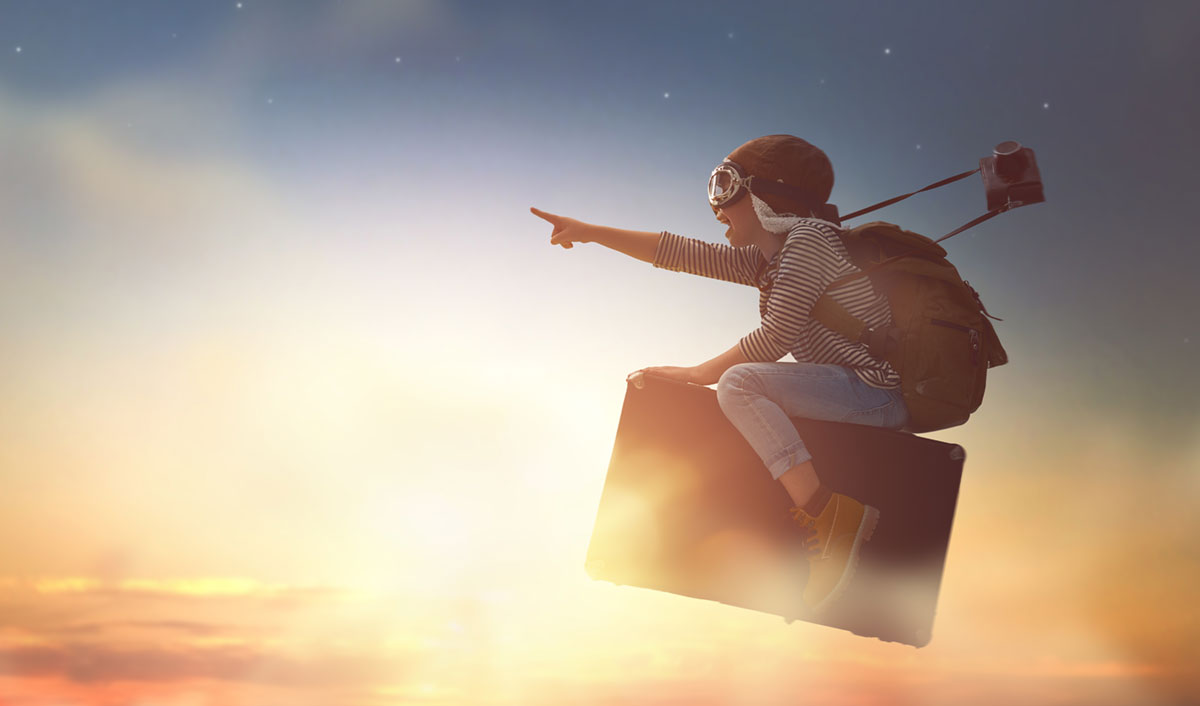
The material receiving area is like a scaled-down version of the entire warehouse. In a warehouse, the action starts at the receiving area and finishes in the shipping area, where goods head out to the marketplace. For receiving itself, the starting point for incoming inventory is the dock and the finish line is when it moves to storage. Between those two points, certain procedures must be implemented to expedite the flow and implement quality control.
Our series on optimized warehouse layouts for small warehouse setup, medium warehouse setup, and large warehouse setup emphasizes the importance of creating an efficient flow for a company’s products, people and machines. Optimizing that flow must begin the moment items arrive in the material receiving area. Problems there trickle downstream and negatively impact operations throughout the warehouse—and ultimately profits. Well-thought-out procedures and layout are a must.
5 Principles of a Successful Material Receiving Area
The same principles for an optimized warehouse will ensure an efficient receiving area:
-
Minimize the number of times an item is touched and the distance it travels.
-
Ensure that the intended path of each product avoids cross-traffic and bottlenecks. Map out and test these routes before operations begin.
-
Establish standard procedures to determine who does what, where, and in what order. Document these processes and communicate them to employees.
-
Automate processes whenever possible.
-
Use appropriate equipment for your space and materials.
The receiving area is just the first stop for materials in the warehouse. In addition to these principles, receiving must also work seamlessly with the processes and objectives of the rest of the warehouse’s operations.
Receiving Area Essentials
Just like a warehouse’s overall setup, the receiving area’s design will be largely dependent on the product and any processes it needs to go through. In some cases, items might go straight from the truck to a storage shelf. Other materials might need to be inspected, counted, sorted, or weighed first.
Most businesses will need at least some basic inspection and organization procedures. They will need to know if they’ve received everything they’ve ordered, that it’s in good shape, and where to put it so it can be found when needed.
For our purposes, we’ll assume that a warehouse’s receiving area includes these basic elements:
-
Delivery
-
Inspection
-
Organization
Everyone has probably moved into a new home at some point. Moving day offers a good analogy for how a warehouse receiving area works. You need to arrange for a moving company or friends to transport and unload your things (delivery), make sure everything arrives and isn’t broken (inspection), determine what goes where (organization), and finally, put it all away where it belongs (moving on to storage).
A warehouse receiving area works in a similar way. Of course, the larger the operation, the more complicated the process. There may be several different tasks and procedures within each of the elements listed above.
Most importantly, each procedure needs to have its own dedicated area. This is the core principle of warehouse receiving set-up. If you do not have separate areas for delivery, inspection, and organization, chances are high that something gets missed.
For example, if there is no specific inspection area, workers may not be able to tell what has and has not been inspected, and damaged goods might end up in storage… and ultimately in the end customers’ package.
Just like moving day, sometimes everything runs smoothly. Other times it’s a logistical nightmare. More often than not, the difference hinges upon the amount of planning and preparation.
Setting Up a Material Receiving Area Layout
Before deciding where things will go and where actions will happen in the receiving area, it must be understood why those things and actions are necessary. What steps are needed to successfully get a product from the delivery truck to its next destination in the warehouse?
Items shouldn’t just be pulled off a truck and stacked wherever there is room. There will be a procedure for unloading and a clear place for items to go. Assign each part of the process a place and someone to perform the task. Make key decisions before operations begin, including:
-
Will you automate with a barcode system?
-
How and when will those barcode labels (or any labels) be applied?
-
Should the labeling station be fixed or on a mobile cart?
-
Will your inspectors go to the products, or will conveyors bring the products to the inspectors?
-
If items must be weighed, you’ll need scales; where will you put the weigh station?
We’ll dive deeper into our three specific areas below. Once you’ve outlined procedures, you can begin designing a map of your layout. This layout will be your best tool to ensure that they are followed and in the correct order.
Finally, don’t forget to communicate these processes to your staff and assign accountability. All of this preparation will ultimately be felt downstream in a number of ways: Mislabelled products can be lost, a box of damaged materials will delay production if it makes it to the manufacturing floor, incorrect counts might cause you to run out of an essential item...and so on.
Bottom line: bad receiving area practices can reverberate all the way through warehouse operations and eventually affect your profits.
Delivery/Unloading
When moving your home, you may hire a moving company or call in favors from friends to get your stuff to your new home. First, you’ll need to let them know when to show up. You’ll want to consider how your large items will get up stairways or around corners. Special equipment like dollies and hand trucks (or just really strong friends!) might be necessary. Finally, know that the longer it takes, the more it will cost you—either in overtime pay for a mover, or more pizza and beer for your friends.
At a warehouse, there are similar things to consider before the first truckload of materials arrives. Physical aspects of the space are important. First, there must be ample room for unloading a shipment and holding items for inspection, sorting, and storage. If pallets need to be broken down, space for that is needed too. In some smaller warehouses, there may be one area that does double duty as both the receiving and shipping area. When this is the case, following proper procedures is essential to compensate for a lack of space.
Consider the delivery method. Unloading needs to happen as quickly and safely as possible. Loading dock doors, ramps, and lifts must accommodate the type of vehicles delivering goods. Will the driver handle unloading, or will your staff? The right material handling equipment is essential too. A hand cart or conveyor might be fine for some items, while pallets will require forklift trucks or pallet jacks.
Scheduling deliveries and including ASNs (advanced shipping notices) in warehouse procedures will ease the receiving process. Delays in unloading can be expensive. Trucking companies often charge detention fees: charges for time a driver waits after a certain allowable grace period. Knowing when deliveries are coming allows warehouse managers to have equipment and personnel in place to ensure timely unloading.
For a shared receiving/shipping area in a small warehouse, scheduling can be a lifesaver. The last thing a company wants to do is impact their outgoing activity. To avoid this, a company may accept deliveries only on certain days or at certain times. Other days or times can be allocated to shipping operations.
Inspection/Quality Control
Employees need a system to ensure that deliveries include the correct items in the right quantities or weight. Processes should be in place to match documentation with the physical inventory. If someone is not comparing the packing slip to the shipment itself, the company could end up paying for things they didn’t get. Errors will be felt down the line when that inventory is missing on the shelves. In our house-moving analogy, a count of boxes would be helpful so you can go back for items accidentally left behind.
Tight procedures to verify incoming materials will allow the receiving department to know immediately if the wrong items or the wrong quantities are on the truck. Suppliers can be contacted and corrections made right away.
Quality control is an important focus when shipping products to consumers, but it is equally important in the material receiving area. Damaged products are useless to a business. If you dropped a box of glassware during your move, you wouldn’t put the broken bits in the kitchen cabinet; you’d take them right to the trash. That’s why a procedure for how to treat unusable items in the receiving area needs to be determined. This is especially important when dealing with fragile or perishable inventory.
Companies typically have allowable damage benchmarks, meaning that they expect a certain percentage of items will not pass their quality control standards. You should designate an area to hold these items until they are either returned or discarded. From there, you can coordinate returns with the vendor or the company’s shipping department.
In large-scale operations, it may be impossible to inspect every single item that comes into the warehouse. Instead, these groups can employ a method of spot-checking that is appropriate for the product. For example, perhaps one of every ten pallets is opened and inspected.
Organization/Labeling
Warehouse management systems (WMS) allow businesses to know the exact location of any piece of inventory at any given time. This begins in the receiving area.
Just like marking moving boxes with the room where their contents belong, organization and labeling in a receiving area saves time, steps, and confusion. A comprehensive labeling or barcoding system dovetails directly into the slotting and rack labeling method used in the warehouse’s main storage area.
An effective procedure dictates how employees are to sort, label, and document materials as they are unloaded at the dock and move toward a put-away area. They will essentially be assigning an address to each item, setting it on a predetermined path to its appropriate place in the warehouse. There, it will await the next step in the manufacturing or assembly process.
Proper cataloging is not just important for inventory control. For example, it can ensure that perishable items use a FIFO (first in, first out) method. It also facilitates locating and removing items that are no longer being used, have reached an expiration date, or are subject to a recall.
Efficient Receiving Sets the Standard
Just as a warehouse must be designed to optimize efficiency, so must all of the areas within. Setting the standards for efficiency begins when a product first arrives in the receiving department. Failure to build an effective flow can hamper operations downstream. Implementing efficient receiving procedures will help set items off on the right foot as they travel through the warehouse.